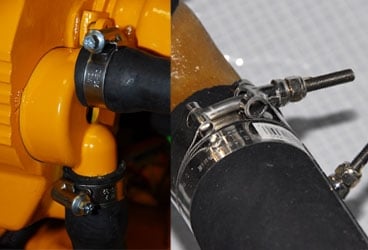
clamps 368
The hose clamp is one of many unsung mechanical heroes aboard your boat. On a routine basis it’s tasked with keeping everything from raw water and exhaust gases to fuel and effluent on the correct side-the inside-of the hoses through which these liquids and gases flow. In an emergency, hose clamps have been used to jury-rig or repair countless onboard items, from broken tiller handles to fractured booms. Why, I once in fact used a handful of clamps and a section of sheet metal to repair a leaking water-injected exhaust elbow.
Clamps come in various styles and in sizes ranging from diminutive to massive. Torque-imparting mechanisms-how you tighten a clamp-also vary. Clamps are made from different materials, which can range from ordinary plated steel to a mixture of different alloys, including stainless steel. The fact is, boat owners face a variety of choices when it comes to buying a clamp for a particular job. But the bottom line is clear: When it comes to keeping water out of a boat or fuel or waste inside a hose, it’s tough to justify anything but the most reliable and durable clamp that you can find.
The familiar helical-screw band clamps have served admirably for years; however, they aren’t without their shortcomings, which are primarily due to the alloy used in making them. The conventional or automotive variety often use a perforated stainless-steel band, in which the perforations are essentially the threads, and have an adjusting screw that’s made from plated mild steel. When the plating is scuffed off or corrodes, the screw rusts, either losing its grip or seizing, which then makes removal of the clamp difficult.
The marine version of the clamp uses a stainless-steel band and screw, eliminating the rust problem. However, in spite of its all-stainless construction, these clamps remain susceptible to crevice corrosion, a form of failure peculiar to stainless steel. (See “Beware of Stainless-Steel Corrosion,” May 2009.) If the clamp is exposed to stagnant, oxygen-depleted water-say, for example, in the bilge-corrosion can set in, causing the clamp’s band to part. This type of failure is especially common on stuffing boxes. The insidiousness of the corrosion is that it occurs on the bottom of the clamp, beneath the stuffing-box hose, where it can’t readily be seen. I’ve encountered this type of failure many times; the clamp looks pristine, but when it’s pulled on, it simply falls off.
The good news is that this type of failure can be avoided. A superior type of marine clamp is made entirely from stainless steel, in some cases 316 alloy, and its band is thicker, making it more resistant to corrosion. Significantly, rather than perforations, its threads are indentations in the band.
Two additional weaknesses of the conventional clamp: It has a tendency to strip the comparatively delicate threads, and because the perforations reduce the overall cross section of the band, it doesn’t take much corrosion to cause the band to part. With the thicker band, these issues are eliminated, making these clamps virtually strip-proof and corrosion-proof.
For larger hoses and higher loads, such as those found in exhaust systems, a different sort of clamp may be pressed into service: the T-bolt. A T-bolt clamp uses a threaded stud and nut rather than a helical screw to impart clamping action, making it well suited to compressing especially thick or large-diameter material. While these clamps tend to be more substantial than their band-clamp brethren, their design makes them susceptible to crevice corrosion, so it’s best to avoid using them in bilges or in areas that remain continuously wet.
Steve D’Antonio, a frequent CW contributor, offers services for vessel owners, boatbuilders, and others in the marine industry through Steve D’Antonio Marine Consulting (www.stevedmarineconsulting.com).