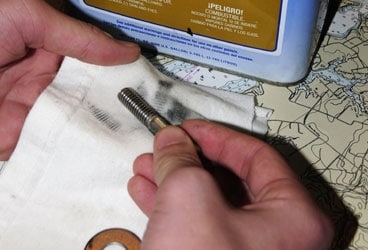
wax and oil 368
Before you install your next piece of hardware or fastener, take a clean, white rag that’s been washed or at least rinsed with fresh water and soak it with mineral spirits or alcohol. (Don’t use the good gin; rubbing alcohol will do.) Then take the new bolt, screw, washer, padeye, cleat, or virtually any other piece of stainless steel and wipe it with your solvent-prepped rag. You’ll be surprised, no doubt, to find black or gray stains left behind.
The aftermath of this wipe down is often cutting oil or wax left when the part was machined or polished. You don’t have to be an engineer or boatbuilder to know that very few things adhere to waxed or oiled surfaces. In fact, when folks who do build or repair fiberglass boats want to form a molded part, they typically apply wax to the mold to aid in the release process. It stands to reason that the last thing you want on hardware that you’re bedding to the weather deck of a boat is wax or oil. Nevertheless, boats are built or repaired every day with deck hardware that’s bedded without being properly cleaned beforehand.
In my work as a boatyard manager and consultant, I’ve encountered countless occasions of leaking deck hardware. Typically, it’s chalked up to defective bedding material, the sealant that’s used to fill the gap between a piece of hardware and the deck. In most cases, however, I believe that the reason for the leak is a failure to decontaminate the hardware and the surface to which it’s being attached.
All hardware, whether it’s made of stainless steel, aluminum, or bronze, should be dewaxed and degreased using either mineral spirits, denatured alcohol, or 3M General Purpose Adhesive Remover. For the dewaxing process, use virgin rags that have been rinsed in clean fresh water. Rinsing the rags first is important, as those from home may have soap or other residue on them, and those that are purchased often are fabric overruns from hosiery or fabric makers. In many cases, they, too, are contaminated, despite their snowy-white appearance.
Once it’s rinsed, soak the rag in solvent, then clean the hardware and surface to which the hardware is to be bedded. Don’t be stingy with rags; once they’ve been used, they should be discarded or washed.
Holes drilled for fasteners should include a chamfer around the side to be bedded, usually the side on deck. This chamfer, or bevel, will help retain bedding compound, forming an O-ring of sorts in the process. Apply bedding compound to the underside of hardware as well as to the fastener heads; however, avoid applying or allowing bedding to contaminate the interior of the fastener threads, the end onto which washers, backing plates, and nuts are installed. The reason for this one-sided bedding approach is to avoid trapping water in the hole through which fasteners pass. When holes are sealed by bedding on both sides, they can retain water, which leads to saturation of the core or to crevice-corroded stainless-steel fasteners.
Finally, don’t use denatured alcohol for cleanup; it inhibits the curing process of many polyurethane bedding sealants. Follow instructions from the bedding manufacturer for preferred cleanup methods and materials.
Steve D’Antonio offers services to boat owners and buyers through Steve D’Antonio Marine Consulting (www.stevedmarineconsulting.com).