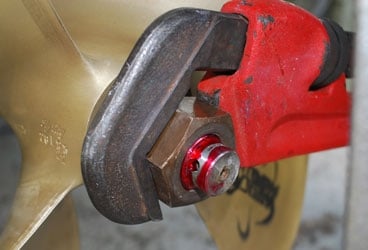
adjustable hex wrench 368
The humble screw and bolt-collectively known as threaded fasteners-hold everything together on a sailboat, from crankshaft bearings and chainplates to VHF-antenna and spar hardware. These connectors are an integral and irreplaceable part of all seagoing craft.
The type of thread on a particular fastener can be separated into two groups: parallel-threaded machine and self-tapping. The former are used in a nut-and-bolt combination and with such threaded hardware as engine blocks and spars. Self-tapping fasteners typically have a tapered thread that, up to a point, is capable of making its own mating threads as it’s screwed into such soft substrates as wood or aluminum.
When it comes to the selection and use of fasteners, among the most important concepts that the user must grasp-and it’s the one that’s most often misunderstood-is torque. In simplified terms, torque represents how tightly parts are joined together with the fastener. In the case of an alternator bracket, for instance, the fastener, typically a hex-head machine screw, joins the bracket to the engine block with enough force that the two can’t move independently. If they’re able to move even a tiny bit, the fastener may hold them together for a while, but it will soon back out completely. Therefore, the primary mission of nearly all fasteners, rather than simply ensuring that components remain attached to each other, is to minimize movement between them. To ensure that fasteners are properly torqued-especially for such critical fasteners as engine and drivetrain components-nothing short of a torque wrench will do.
A seemingly endless variety of fastener heads, together requiring an equally endless variety of screwdrivers and wrenches, are employed aboard the average cruising sailboat. The most common remains the hex-head cap screw or bolt. These are best driven using socket, box, open-end, and adjustable wrenches, in that order. Force placed simultaneously on all six sides or flats of a hex head offers the least likelihood of slippage or cam out, which is commonly called stripping, although this term should be reserved for damage to or the failure of threads.
Sailors may encounter several other heads and drive types, including socket-recess (also known as Allen), Frearson, square, square-recess (also known as Robertson), Torx, and Security Torx drives, to name just a few. If you intend to work on the gear aboard your vessel, you must have the tools to install and remove these fasteners. Few situations are more frustrating in the world of things mechanical than not being able to disassemble a component because you don’t have the proper tool.
Among the most common failures involving machine-thread fasteners is unintended loosening. This is commonly the result of a combination of factors that can include improper torque, vibration, and failure to use a locking device. To prevent a fastener from becoming loose, particularly critical ones such as those used on engines, couplings, and rigging, tighten it with a torque wrench. Also, use a high-quality locking device such as a split or star lock-washer. For critical systems or those subject to extreme vibration, consider using a Nord-Lock washer (www.nord-lock.com) or a thread-locking compound, such as Loctite 242 or 271 (www.loctite.com).
Select your fastener wisely, based on its intended use and the anticipated loads. Be certain that you have the proper tools both to install and to remove it. And whenever possible, use a torque wrench, especially when working on critical components.
Steve D’Antonio is a regular CW contributor and offers services for vessel owners, boatbuilders, and others in the marine industry through Steve D’Antonio Marine Consulting (www.stevedmarineconsulting.com).