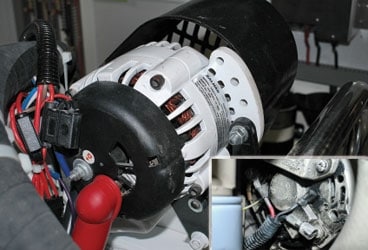
tight alternator connections 368
Much has been written about marine DC-charging systems, and with good reason: When they fail, they can leave the average cruising sailor without battery power for the lights or engine just when it’d be appreciated the most. This month, however, I’ll try to clarify some of the maintenance-related mysteries behind the machinery that keeps your batteries charged up and full of life.
The essence of the DC-charging system is, of course, the alternator. While shore-powered chargers are a valuable source of energy, they don’t do you very much good once you’ve left the dock (unless you have a generator). The alternator, then, is the primary means of keeping the batteries topped off while you’re under way. For that reason, it must be properly maintained to ensure its maximum longevity and reliability.
Alternator failures are often the result of one or more common problems. In many cases, the alternator’s drive belt is improperly adjusted. (For guidelines to make proper alternator adjustments, see “An Orderly Transfer of Power” in CW‘s October 2006 issue.) If the belt is too loose, the alternator won’t spin fast enough to provide its maximum charging output. Perhaps more important, however, is that a slipping alternator belt will often cause the alternator’s pulley to overheat. If you’ve ever seen an alternator pulley that has a blue or purplish hue, it’s one that’s suffered from chronic slippage and overheating. The overheating won’t only cause the belt to fail prematurely; the heat can actually migrate along the alternator shaft and into the rotor’s magnets. Once overheated, these magnets will be weakened, and the alternator’s output will be permanently diminished.
With the increased popularity of electronics and the reliance on high-output alternators, bracket failures have become more common. If an alternator bracket’s design allows it to flex and vibrate, then its demise is almost assured. This happens when the bracket’s metal and welds repeatedly flex with each vibration cycle; this flexing causes the bracket eventually to fail. If your alternator vibrates while the engine is running-it should move with the engine’s own natural or unavoidable vibration rather than independently of it-then its bracketing needs to be reinforced or redesigned. Additionally, even if an overly flexible alternator bracket doesn’t fail, it often moves enough under ordinary belt tension to create misalignment. When this occurs, the belt or belts will suffer from rapid wear, which is frequently evidenced by an accumulation of belt dust. Not only must the alternator and crankshaft or drive pulleys be parallel; they must also reside in the same plane in order to avoid excessive belt wear.
Another frequent cause of alternator failure involves, not surprisingly, its wiring. Because some vibration and movement of an alternator is unavoidable, it’s especially important that its wiring be secure, have appropriate slackness, and be durable. Check all of the wiring that’s connected to the rear side of your alternator. The nut on the output stud should be properly tightened and locked in place using a nylon locking nut or lock washer. Loose connections often lead both to arcing between the output stud and the cable and to overheating.
With a little care, your alternator should prove to be reliable and free of trouble for thousands of engine-operating hours.
Steve D’Antonio is a regular Cruising World contributor who offers services for vessel owners, boatbuilders, and others in the marine industry through Steve D’Antonio Marine Consulting (www.stevedmarineconsulting.com).