Imagine it’s 1931 and you’re looking for a new 85-horsepower marine diesel. That year, Caterpillar offered a state-of-the art machine that might do the trick—except for one not-so-small detail: It weighed 5,175 pounds. Today, you can buy an 86-horsepower diesel that weighs a mere 580 pounds. The differences between your own 15- or 20-year-old diesel engine and its modern equivalent aren’t nearly as extreme, but if you’re planning to repower, an understanding of current trends in marine diesels will help you make a seamless engine switch.

|

|

| |

|
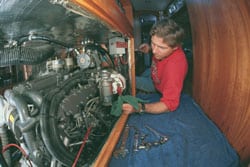
|

| |

|Michael Eudenbach|

| |

|

|

| |

|A key consideration when repowering is whether your existing engine space will allow for easy access to the new engine’s service points.* * *|

| |

|

|

|
Twenty-five years ago, some marine diesels were made specifically for the marine market. They were produced in low numbers, raw-water cooled (cooled by circulating water from outside the boat through the engine), and designed with heavy castings to last in the marine environment. Their heavier mass allowed for smooth running, and their relatively low rpm minimized bearing wear. Many are still going strong today.
Although a large number of raw-water-cooled engines are still in use today, virtually every new auxiliary diesel has a closed cooling system, in which coolant recirculates through the engine block (see “Can Your Cooling System Take the Heat?,” September 2001). Aside from mitigating the obvious problem of corrosion, a closed cooling system allows for a higher operating temperature, which in turn permits more complete and efficient combustion.
Nearly every modern marine diesel is built around an industrial block engineered primarily for use on land. All have internal flywheels, and a good number of them run at 3,600 rpm or higher. Except in a few cases, each marine-engine manufacturer marinizes the basic block by adding the components required for marine use. Some components are generic, off-the-shelf parts (alternators and raw-water pumps, for example); others are custom designed and fabricated specifically for each engine model (exhaust manifolds). To save weight and combat corrosion, these engines use more aluminum alloys, bronze, and stainless steel rather than cast iron or steel. In some power plants, you’ll find more exotic alloys, such as Almag 90 (a magnesium-aluminum alloy used by Westerbeke for exhaust elbows and manifolds). Plastic parts are common, especially for such light-duty applications as belt guards and air-intake baffles.
With the help of computer-controlled design, foundry operation, and machining, manufacturers have also made good progress in reducing noise and vibration. Turbocharging (essentially force-feeding air into the air-intake port) a diesel of any size will also mitigate some combustion noise that would otherwise escape through the air-intake baffle. Some engine manufacturers include counterrotating shafts within their engine blocks that offset the reciprocal tiny vibration caused by piston and crankshaft movement.
A small but important detail is the improvement in isolators, or motor mounts. In days of old, these were designed simply for attaching the engine block to the stringers. Some older installations that eliminated the mounts altogether not only rattled the boat and crew; other gear on board would resonate with the vibrations, adding higher notes to accompany the drone of combustion. Most modern engine mounts specify a different hardness for the front and back (to counter transmission weight) as well as for the left and right sides (to counter torque) of the engine.
Fuel Efficiency
Thanks to the U.S. Environmental Protection Agency, modern diesel engines are more fuel efficient and environmentally friendly than those of just 10 years ago. In 1997, the first stage of a three-stage program to reduce diesel exhaust emissions took effect. Stricter Tier 2 standards are now being phased in. Engines between 25 and 50 horsepower must comply by 2004. For engines up to 25 horsepower, Tier 2 standards start in 2005. Meanwhile, you’ll find Tier 2-compliant and Tier 2-noncompliant engines in both sizes. The most stringent criteria, Tier 3, takes effect in 2008, and will apparently only apply to engines above 50 horsepower. Compliant engines will generally cost 1 to 3 percent more than ones that haven’t yet been upgraded; in my opinion, it’s worth paying a little more for a cleaner, more efficient power plant.
If they haven’t already, most manufacturers will meet the mandate in their smaller engines by tweaking existing systems—for example, by increasing fuel-injection pressures or modifying cooling systems. However, engines that must meet the stricter Tier 3 standard—those above 50 horsepower—will, in all likelihood, do so by adding turbochargers and after-cooling. (After-cooling cools the air after turbocharging and prior to intake, making it more dense and allowing for more efficient combustion.) Depending on the horsepower of your next diesel, a turbocharged engine may soon be your only option.
With the quest for better efficiency and simpler, less expensive components, rotary injection pumps have become more popular during the past 20 years. You can recognize rotary pumps by their high-pressure fuel lines, which exit the pump horizontally; in in-line jerk pumps, the lines exit vertically from the top of the pump body. Most modern rotary pumps employ an electric solenoid to enable the fuel supply. This simplifies installation for boatbuilders, but the solenoid can fail, leaving a boat dead in the water. In-line jerk pumps might also use an external solenoid to shut down the engine, but you can easily bypass a bad external solenoid. Some manufacturers still offer engines in which stopping the engine remains an all-mechanical affair, but these are becoming less common. Solenoid failures notwithstanding, rotary injection pumps are typically quite reliable and long-lived. They are also less sensitive than jerk pumps to contamination and imprecise calibration.
In general, fuel systems have become more user-friendly. Most engines today have spin-on secondary fuel filters, which are much easier to service and bleed than the dreaded sandwiched canister types, and they offer simplified means for bleeding and priming the fuel system. Some engines even offer what are called self-bleeding fuel systems, a real boon to the wrench-wary skipper.
Electrical Systems
Another change that distinguishes today’s diesels from those of the past is their auxiliary electrical equipment and wiring. Engine installations used to be custom. Each wire for the key switch, instruments, and alternator was attached by the installer, whose handiwork may have been less than perfect.
Today, nearly every production auxiliary diesel is plug-and-play. Utilizing this modular wiring system, every wire, with the exception of the heavy-gauge starter cable, is prewired and checked at the factory. The installer simply plugs the engine’s wiring harness into the other half of the harness, which is prewired to the instrument panel, and hooks up the starter supply cable. However, if the molded plug at the harness union gets wet, corrodes, or loosens, the engine’s electrical system will fail. I have, on occasion, had to replace these plugs with old-fashioned terminal strips because they were corroded beyond repair. You can avoid this problem by routinely separating the plug and, if necessary, cleaning the contacts before reassembling it. Coating the plug lightly with dielectric grease will also help keep moisture out.
Preheat systems, which make cold starting easier, have also greatly improved. I have bad memories of the old blowtorch system that dribbled fuel over an electric heating element stationed within the intake manifold. Today, long-lived glow plugs or intake air heaters do the job without fuss. These are still manually activated on most sail-auxiliary diesels. However, larger “electronically controlled” diesels have replaced the manual system with an automatic pre- and post-heating system, which not only makes starting easier but reduces white smoke as well.
So what will diesel engines look like in the near future? We can well expect the ratio of horsepower to pound of weight to continue to rise. The 1931 Caterpillar that I mentioned earlier produced 1 horsepower for every 59 pounds of engine mass. A modern sail auxiliary diesel produces that same 1 horsepower for every 10 to 15 pounds or less of engine weight. An increase in rated rpm and the proliferation of turbochargers are just two of the reasons for this horsepower leap. But as you’ll see from the selection below, the range of midsize engines still includes a number of slower-turning models, and natural aspiration is still the norm.
Repowering in 2002
Realistically, North American sailors searching for a new marine diesel in the midsize horsepower range (30 to 60 horsepower) don’t have a wide selection of manufacturers from which to choose.
The big three diesel makers who cater to U.S. cruising sailors are Yanmar, Volvo Penta, and Westerbeke (which also produces Universal engines). Above 60 horsepower, Cummins and Caterpillar/Perkins Sabre enter the picture. Caterpillar recently purchased Sabre, the British company that built a loyal following with its marinized Perkins engines. As you read, yellow-painted Perkins Sabres with the Caterpillar name are rolling out of Sabre’s plant in Dorsett, England, along with same engines stamped Perkins Sabre. Though the engines are virtually the same, each brand will also have its own parts numbers and service manuals, among other things, and will be backed by its own support, sales, and training programs.
Choices outside the mainstream include several makers of marinized midsize diesels: Betamarine (based in the United Kingdom; they marinize Japanese Kubota diesels), Vetus den Ouden (the Netherlands; they marinize Mitsubishi diesels), Deutz (Germany), Nanni (France; they also marinize Kubotas), Bukh (Denmark), Volkswagen (Germany; they recently announced a new line of marine diesels), Lister-Petter (United Kingdom; they’ve recently teamed up with Norway’s SABB Motors), and Farymann (Germany; they build small marine diesels). A handful of smaller companies in the United States also convert popular diesels for marine use. Among them are Norpro (Massachusetts; they marinize Isuzu diesels) and Phasor (Florida; they marinize Kubota diesels).
The advantages of sticking with an established marine business are clear: The manufacturers know how we use (and misuse) our engines; service centers are responsive to sailors’ needs; the warranty applies specifically to marine use; mechanics are more widely available; and there’s a greater chance that your engine maker will still be stocking parts 10 years from now.
If you’re repowering, one of your first questions will be about how to match an engine’s power to your boat’s displacement. Such books as Francis S. Kinney’s Skene’s Elements of Yacht Design (1973; G. P. Putnam and Sons; $29.95) offer tables, but a general rule of thumb is to figure between 2 and 2.5 horsepower for every 1,000 pounds of displacement when the boat’s fully loaded. For this grouping, we focus on four-cylinder engines of around 50 horsepower, a fair match for a 35- to 40-foot medium-displacement cruising monohull. Here’s a rundown of what companies have to offer:
Betamarine BV2203: In production for about 10 years, this is a marinized version of the efficient, low-revving Kubota V2203. An ample, well-balanced flywheel ensures stable operation and higher torque than any other engine of its size in this group: 115 pound-feet at 1,800 rpm. The high torque is ideal for a heavy-displacement hull with a big, three-bladed propeller. A suitable replacement for a variety of engines, including the Perkins 4-108, the BV2203 is relatively compact. At 20.8 inches wide, it’s the second narrowest engine in this field. Betamarine’s primary distribution network includes four locations in the United States, wide representation in the United Kingdom, and suppliers in more than 60 countries worldwide. Kubota has a good reputation for producing durable engines that are suitable for marine conversion.
Perkins Sabre M65/Caterpillar 3034: Introduced in 1998, this 3.0-liter engine lies beyond our horsepower range, but it’s the currently the smallest engine coming from Perkins Sabre (and now Caterpillar) and worth a look for those seeking a little extra power in a slow-turning, naturally aspirated engine. It’s only slightly longer (39 inches total) than the other engines in this group. It replaces the popular Perkins 4-108 and 4-107, and the engine mounts and brackets simplify repowering. Key service points are located on the engine’s starboard side, except the water-pump impeller, which is on the port side. An in-line jerk pump supplies fuel. The fuel filter isn’t the spin-on type. Perkins is supported by over 4,000 distributors in 160 countries, and Caterpillar’s reach is equally broad.
SABB-Lister 4 x 90: The marinized version of the Lister-Petter X series, originally designed for low-profile loaders used in narrow mineshafts, debuted this June. Only 25 inches high, the 4 x 90’s total volume is the least of any engine in this group. Weighing more than the other engines in its horsepower range, it has plenty of torque at low rpm. A protected crankcase-oil-pressure system allows it to work continuously at a 30-degree angle. The engine has a range of flexible mounts to suit various installations. For several years, SABB Motor (not to be confused with the Swedish automaker Saab) has been marinizing Lister engines for lifeboats as well as for more conventional marine use. Lister-Petter has a long history of powering boats in Europe. According to SABB, the 4 x 90 will be backed by Lister-Petter’s worldwide network for sales, parts, and service, but for American sailors, this is clearly the rarest bird in this group.
Universal M-50B: Although it falls short of our 50-horsepower criterion, the M-50B, introduced in 1998 to meet the new EPA emission standards, merits a look from those shopping in that range. A Kubota engine marinized by Westerbeke, the clean-burning M-50B produces 42 horsepower at 2,800 rpm. The engine will appeal to cruising sailors looking for a quieter engine that operates efficiently at low rpm. Handy features include Westerbeke’s self-bleeding fuel system, a circuit breaker built into the starting system, and a built-in oil-sump pump. The fuel pump is a Bosch in-line model, and the fuel filter is the spin-on type. With virtually the same dimensions as its predecessor, the M-50, the M-50B is a suitable replacement for a wide range of engines, including the Westerbeke Four-99, Four-107, Four-108, W-40, and W-50. Universal is backed by Westerbeke’s wide distribution network. The company provides comprehensive service manuals and a variety of spare-parts kits for cruising.
Volvo Penta D2-55: Introduced last year, the 2.2-liter D2-55 incorporates Volvo Penta’s proven experience in marinization into a reliable, well-engineered Perkins engine. It’s one of the slow-turning, high-output engines in our group. With a relatively big internal flywheel and efficient isolation (through high-density rubber mounts), the engine runs quietly at low rpm. Successor to the popular MD-22 series, the D2-55 is the second-smallest engine in our group and will also fit neatly in place of the Perkins 4-108. The injection pump is of the in-line, cam-driven variety, and the secondary fuel filter is the convenient spin-on type. The water-pump impeller is easily accessible at the front of the engine. The engine is set up to accommodate hot-water-outlet fittings and two alternators. Builders that use Volvos include Beneteau, Bavaria, and Swan. Volvo Penta has an extensive worldwide parts and service network and offers a variety of spare-parts kits tailored for cruising sailors.
Westerbeke 55A: Debuting in 1995, the 2.2-liter Westerbeke 55A is based on a Mitsubishi engine, a make that for two decades Westerbeke has successfully converted for marine use. A self-bleeding fuel system simplifies operation, and spin-on secondary fuel filters ease maintenance. The injection pump is the rotary type. It’s a quiet engine in comparison with its predecessors, and it comes with installed connections for a water heater. It also features lube-oil and transmission-oil coolers. The exhaust elbow is of the clamp-on variety, avoiding problems with fused threads when the time comes for servicing or replacement. Valiant, PDQ Yachts, and Sabre are among builders that have used the Westerbeke 55A in their new boats. Based in Massachusetts, family-run Westerbeke is well represented in the United States and Canada, provides a convenient online store for ordering parts from anywhere, and has over 65 distributors around the world.
Yanmar 4JH3E: The 1.9-liter Yanmar 4JH3E, introduced in 2000, is a pure marine diesel specifically designed from the block up to meet the demands of today’s boaters. It’s the biggest-selling engine in this group, so it offers the widest service backing worldwide, with distributors in 130 countries. It’s also the fastest-turning, highest-output engine in our under-60-horsepower group. The spin-on fuel filter is readily accessible at the front of the engine. With a compact cast-iron block and head, as well as extensive use of aluminum alloys in the oil pan, covers, and many parts, the EPA-compliant 4JH3E is 6 pounds lighter than its predecessor, the 4JH2E, yet delivers 5 horsepower more. The high-pressure fuel-injection system, freshwater cooling, and exhaust system are all built by Yanmar. The size envelope is almost identical to the old Perkins 4-107 or 4-108. Yanmar offers a variety of transmission options for the 4JH3 (the E suffix denotes a parallel drive), including sail-drive and down-angle versions, as well several choices of mounting brackets.
Steve D’Antonio is the service manager at Zimmerman Marine in Cardinal, Virginia. CW associate editor Darrell Nicholson contributed to this article.