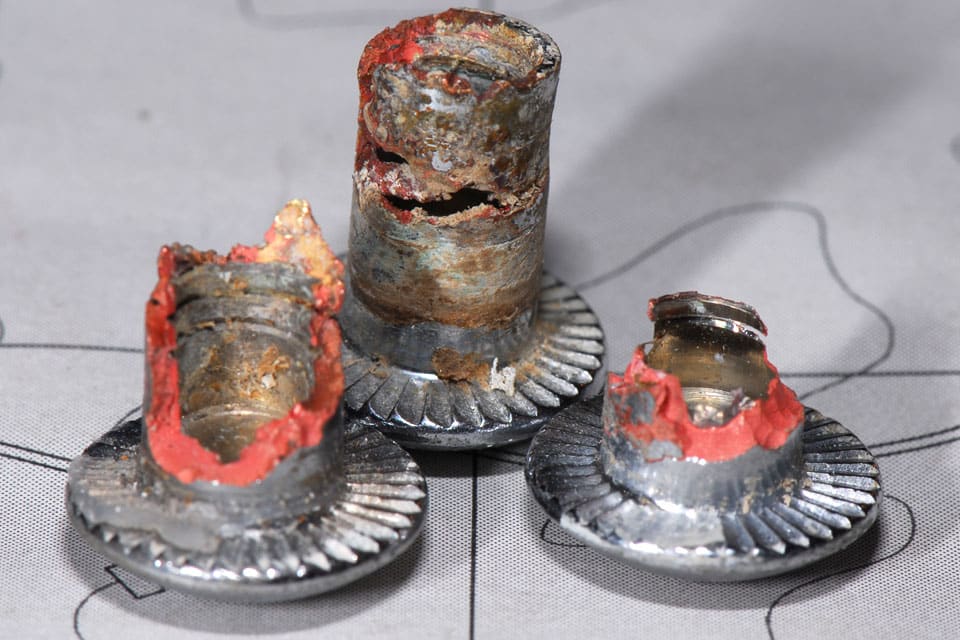
Corroded brass
Untreated brass is an alloy that’s routinely used for a variety of nautical applications—like clocks, barometers, and cabin fittings—and develops an essentially harmless greenish-blue surface patina. However, when used incorrectly, in applications for which it isn’t intended, brass’s warm characteristics can change catastrophically.
Brass is primarily made up of two elements, copper and zinc. While corrosion resistant, copper is soft and not well suited for structural applications. Once alloyed with zinc, however, its tensile strength increases significantly, making it rigid enough for hardware and plumbing applications, with some critical exclusions.
Brass alloys come in a wide variety, all with varying percentages of copper, zinc, and other elements. These alloys include red brass (85 percent copper, 15 percent zinc), leaded red brass (85 percent copper, 5 percent zinc, 5 percent lead, 5 percent tin), admiralty brass (70 percent copper, 30 percent zinc), naval brass (60 percent copper, 40 percent zinc), aluminum brass (76 percent copper, 22 percent zinc, 2 percent aluminum), and manganese “bronze” (60 percent copper, 28 percent zinc, with the remainder consisting of manganese, iron, and lead); because of its zinc content, manganese bronze actually resides in the brass family.
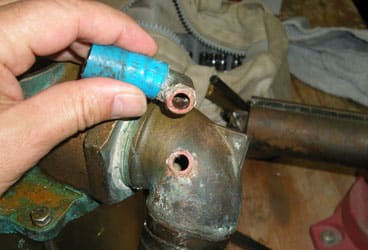
| |This 90-degree pipe-to-hose adapter parted from the larger brass fitting to which it was attached with little effort. The telltale pink hue is a clear sign that this brass has “dezincified.”|
While brass works well in the aforementioned above-the-waterline applications, it’s certain to fail when put to work in situations that leave it constantly exposed to seawater. Because of its high zinc content, brass suffers from a peculiar type of corrosion known as dezincification; when this happens, the zinc sacrificially corrodes from the alloy, leaving behind a porous, weak copper structure that deceptively retains its shape yet is devoid of most of its original rigidity. Such fittings are often pinkish, and they can often be easily broken with minimal effort. Because it had the telltale pink appearance, I once grabbed the water-injection fitting for a stuffing box to test its strength—and it instantly separated from the larger fitting into which it was screwed. Fortunately, the boat was hauled at the time.
Don’t be fooled by such alloys as admiralty brass and naval bronze, which sound like they should be corrosion resistant. Due to their relatively high zinc content, these are indeed brasses, and they shouldn’t be used in plumbing applications below the waterline or involving seawater. Propellers and some rudder-hardware components are made from manganese bronze; it’s important to protect these with zinc or aluminum anodes to prevent dezincification.
Frustratingly, it’s nearly impossible to determine the difference between brass, bronze, leaded red brass, and DZR (for “dezincification resistant brass”) alloys, the latter three of which are all acceptable when used below the waterline or in seawater. With regard to content, I’m uncomfortable for seawater use with any alloy that contains more than 10 percent zinc. Seacocks that meet ABYC standards H-27/UL 1121 and are so labeled (European seacocks may be labeled “DZR”) are perfectly fine. Otherwise, however, there’s no way of knowing—regardless of the label on the bin—the zinc content of a 3/8-inch pipe nipple or a 1/4-inch pipe plug that you pick up off the shelf at the local chandlery. Such easily fabricated, smaller-size plumbing parts as these are routinely made from brass, while bronze must often be special ordered. So purchase parts from reputable suppliers, including seacock and strainer manufacturers, and remain vigilant for signs of dezincification.
Steve D’Antonio assists boat owners and buyers through Steve D’Antonio Marine Consulting (www.stevedmarineconsulting.com).