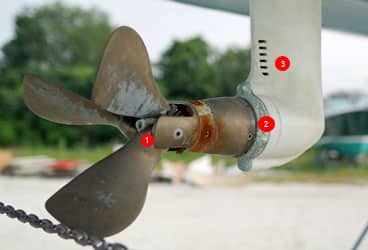
So, how’s your drive? I’m not talking about your daily commute or personal energy level here. I’m talking about your saildrive, if you have one. Increasingly, boatbuilders are adopting saildrives over the traditional shaft and propeller, and with good reason: They’re much easier to install, and they offer a considerably quieter ride when the wind dies and you simply must fire up the diesel. During CW‘s Boat of the Year competition in 2009, for example, a third of the new boats we looked at were equipped with saildrive propulsion, so they’re here to stay. And though early adopters of the drives experienced some well-publicized problems, the technology has evolved considerably since then.
I can remember some of the conversations with my colleagues when saildrives first appeared. Thoughts of failure of the rubber bladder that seals them to the hull were at the top of the list of why they were a bad idea. Some of us had lingering memories of Outboard Marine Corporation’s early attempt at offering saildrive functionality, basically by using an outboard-engine power head with a lower unit mounted inboard. They were very problematic and only lasted a few years before they disappeared into the not-such-a-great-idea department.
Well, we’re past all of that. Today, both Volvo Penta and Yanmar offer complete saildrive solutions. The initial fears of rubber-bladder failure are simply no longer an issue. I haven’t heard of one case in which this has occurred. Certainly this is a maintenance item that needs addressing at some point, but premature failure has not been a factor.
What has been a factor is rampant corrosion of the aluminum drive units, with total replacement—at great expense—sometimes required. In some cases, the rapid decay has been so severe that drives appear to have dissolved off the bottom of the boats to which they were fitted. Many online forums and discussions have addressed this problem, and much misinformation about the causes for this corrosion has been distributed widely. I hope to end much of the confusion right now.
Anode-to-Cathode Relationship
The essence of the problem centers around one basic corrosion-mitigation premise: that there exists a proper relationship between the surface area of the anode, typically a zinc or aluminum-alloy fitting, and the surface area of the cathode, which includes the saildrive, the propeller, and any other metal below-the-water fittings. What this means simply is that the amount of metal exposed to the electrolyte (the water in which the boat floats) must be proportional to the amount of sacrificial anode installed on the boat.
It’s important to remember here that drive manufacturers install anodes on their drive units at the factory that are intended to protect the drive units only as shipped with their standard propeller. Let me repeat that: The anodes supplied are engineered to protect the drive units and standard props only. Many sailors will add a bronze feathering propeller to the drive, which means that more anode area is going to be needed, though too often this is overlooked. This simple alteration is going to decrease the anode service life because more cathode area has been added. Additional bronze through-hull fittings may also be added, again requiring additional anode surface area.
On several boats I’ve inspected after the damage was done, lead or cast-iron keels had been exposed to seawater due either to faulty paint systems on the metal keels or, in one case, because the owner was racing the boat and had wet-sanded the epoxy barrier coating on the lead down to bare metal. In any of these cases, the anode-to-cathode surface-area relationship had been altered, and insufficient anode area caused the factory-installed anodes to dissolve quite quickly, in a matter of weeks instead of months. Remember that the next bit of metal in the corrosion food chain after the anodes is the drive casing itself, which, made of aluminum, is far more susceptible to anodic action than bronze through-hulls or other fittings.
The Cathodic Protection System
To fully understand the cause of this corrosion, you need to understand how and why a properly designed cathodic protection system works. The system begins by tying all of the underwater metals together electrically via a bonding system. On most boats, this is accomplished with green insulated wire, sized 8 gauge or larger. What happens next is an electro-chemical process known as polarization of the metals. You see, all metals when submerged in an electrolyte solution (such as salt water) have a voltage potential. Potentials vary depending upon the specific alloy used. By electrically connecting all of the various alloys, once polarization occurs, the voltage potentials equalize. Anodes need to be tied to this same bonding system, and the anode material must have a voltage potential at least 200 millivolts more negative than the rest of the system. The anodes then become the sacrificial component within the system; enough anode mass needs to be added to ensure satisfactory service life, which is generally considered to be six to nine months. At that interval, you need to install new anodes.
Hey, It’s the Neighbors
Essentially what’s being created with this bonding system is what we call a galvanic cell, with an anode and cathode connected electrically and both submerged in the same electrolyte solution, in this case, the water around your boat. Think of it as a giant battery. Low-level current flows from the more negative anode to the cathode, but because each element of the cathode has undergone polarization, their potential voltage is equal, so none experiences corrosion. Instead, the anode slowly wears away.
Remember that there has to be a difference in potential for current to flow. That’s the operating premise behind bonding; if all of the potentials are equalized due to polarization, there can be no current flow between the individual elements. So a boat with proper anodes, sitting in a lone anchorage or on a mooring, isn’t likely to suffer from galvanic corrosion.
But what about boats in a marina? That’s a whole nother story. The issue at hand is that the green wire that ties the metals on a boat together is a part of the overall grounding system and, so, is also connected to the boat’s shore-power grounding system. The significance of this is that whenever your boat is plugged in to shore power, it means that you’re electrically connected to all of your dock mates via the green wire, which is continuous throughout the entire dock.
Because of these continuous links among all the boats, your boat’s anodes may actually be helping to protect one of your dock mates from corrosion, putting a heavy demand on your boat’s anodes and causing accelerated anode depletion. In other words, the boats around you are causing your anodes to wear away faster than you might expect; hence, your saildrive is unwittingly put at risk.
To mitigate this problem, you must have a galvanic isolator installed in your shore-power system. In essence, this device is installed in series with the green wire in your shore-power wiring, in accordance with the American Boat & Yacht Council’s Standards, Section E-2: “Cathodic Protection Systems.” The galvanic isolator works by blocking low-level galvanic current, but it allows the passage of AC fault current in the green wire if called into action due to an AC-system short circuit. It’s important to remember that by removing any one of the components of a galvanic cell, which needs an anode, cathode, a hard-wire connection between the two, and an electrolyte, you stop the corrosion process. The galvanic isolator blocks the hard-wire connection to others in the marina, leaving your anodes to work for your boat alone.
A new trick that some of us who are involved with marine-corrosion issues are now employing involves using a galvanic isolator installed in the green-wire link from a saildrive and engine to a keel bolt, and hence the keel, since these metal components are in most cases connected via the bonding system. This installation effectively isolates the keel, from a galvanic perspective, from the drive in the event that the keel does lose any of its protective barrier coating. (More on coatings in a minute.)
Choose the Correct Anode
Although most people refer to their anodes as “zincs,” they may not be made of zinc, and using the correct anode material for given water chemistry is, in fact, of paramount importance. Anodes come in three basic materials: zinc, aluminum, and magnesium. All three are actually very specialized alloys of each of these metals, and they’re designed to achieve appropriate voltage potentials in salt water, fresh water, and brackish seawater.
The proper selection of anode material can’t be overstressed. One fellow who lost several saildrives finally found out that the zinc anodes installed at the factory on his boat weren’t really doing anything to protect against corrosion in the brackish water in which he kept his boat. In fact, aluminum anodes would’ve been the preferred choice.
The reason for this difference in material selection centers around the relative conductivity of the water in which your boat sits. Salt water is quite conductive, so zinc anodes, which have an electrical potential of around -1,050 millivolts, work just fine. Brackish water is quite subjective depending upon its salinity, so aluminum anodes, with a voltage potential of -1,100 millivolts, perform better due to their slightly higher voltage potential; these actually can also be the best choice in salt water. In fact, most outboard-engine makers now supply these as standard equipment, not knowing where the engines will be used. Magnesium, which should only be used in fresh water, can have a negative voltage potential up to around -1,630 millivolts; it can be quite damaging to aluminum if used in salt water.
The Importance of Coatings
One of the most important components in the mitigation of corrosion is the proper type and application of protective metal coatings. Proper coating effectively insulates metal from the electrolyte surrounding it, again eliminating one of the components necessary to complete the galvanic cell. On a drive unit on which this coating is beginning to be compromised, this puts a higher demand on the anodes, and once they’re depleted, the drive begins to corrode rapidly.
The best base coatings we have available to us today are any of the epoxy barrier coats available, such as Interlux Interprotect. Apply this to all underwater metals, including bronze through-hulls, before any anti-fouling coating goes on. On drives that have already been submerged in salt water, another hidden enemy lurks: soluble salts, which are invisible and tasteless. These microscopic particles cause premature paint-system failure and must be cleaned away before any epoxy or paint is applied. The trouble is, these particles are difficult to clean off. In fact, a typical boatyard pressure washer won’t remove them. Yanmar, for example, recommends both a test kit and a biodegradable neutralizing wash made by Chlor-rid Corporation (www.chlor-rid.com). If you’re recoating a saildrive, this step is super important to ensure that the coating stays on the aluminum.
The primer and anti-fouling are important too. Don’t use any anti-fouling paint containing copper on a saildrive. Yanmar says that the Interlux Trilux 33 system or its equivalent should be used.
The Final Check
You must perform a final check to be sure that you’ve achieved the proper level of cathodic protection. You can do this yourself by using a standard multimeter/silver-chloride reference-cell combination instrument. To do this, make sure your boat is unplugged from shore power. Set your multi-meter to the DC-volts scale. Connect the positive lead from your meter to the boat’s grounding buss (the one to which all the green insulated wires are attached). Submerge the reference cell in water to the same approximated depth as the installed anodes on your boat. If all is well, you should see a negative voltage reading of between -950 to -1,100 millivolts. If the reading is too low—that is, less than -950 millivolts—then you need more anode surface area.
My recommendation is to employ the services of an ABYC-certified corrosion technician to perform what’s known as a Hull Potential Test. Do the test only after the boat has been floating in its usual location for several days. The polarization process doesn’t occur immediately; it usually takes 24 to 48 hours. The correct level of cathodic protection will vary depending on hull material and how your boat is configured. To get an idea of the range of voltages the tester should get, see “Recommended Range of Cathodic Protection for Boats with Saildrives” (left).
Remember that the initial reading when all anodes are new should be toward the more negative, say, perhaps, -1,100 millivolts. This is because as the anodes deplete, the voltage range will shift to a more positive number, eventually indicating under-protection. It is also quite important that the number not be any greater than -1,100 millivolts in order to protect your saildrive. Aluminum is somewhat unique among marine metals in that it can be easily overprotected or underprotected cathodically, and in either case, damage to the casting will occur. Sometimes this happens quite rapidly.
To sum up: If you follow the advice here, your drive should give you many years of good service. But I must emphasize: Diligence is of paramount importance. Don’t let anyone tell you that six to eight weeks of anode life is acceptable; this is a common depletion rate only when something is wrong.
Ed Sherman, the curriculum director for the American Boat & Yacht Council, was a 2011 Boat of the Year judge.