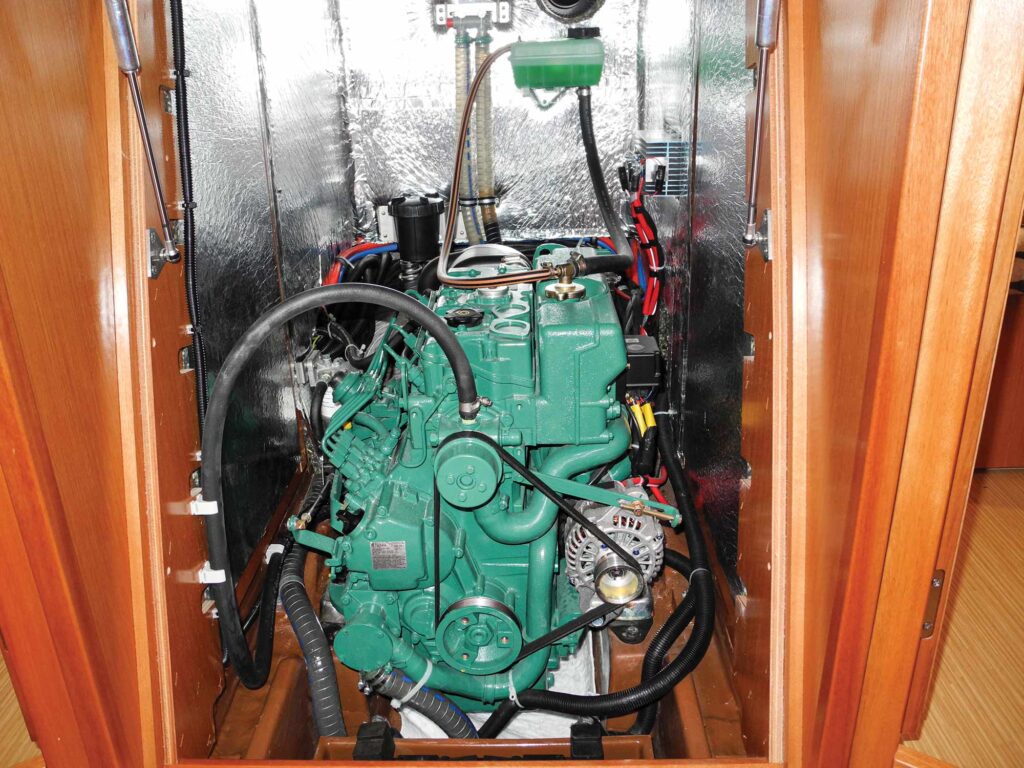
If you are planning to do any cruising that takes you away from your dock or mooring for even a single overnight, there are five things that you simply must know how to do on your diesel engine.
1. Replace the Fuel Filter
Diesel fuel is prone to contamination and water accumulation, especially in the marine environment. Diesel fuel, unlike gasoline, can actually support microbial growth, often incorrectly referred to as algae. That black slime is a microscopic goo of “bugs” that can thrive in a boat’s fuel tank. Typically, they live right at the line where water in the fuel and the fuel itself meets.
The water will always settle to the bottom of a filter assembly. It is imperative that a diesel engine be equipped with two fuel filters: a primary and a secondary. You need to know how to service these filters when the worst happens, should they become waterlogged or clogged with contaminants.
Filter elements are among the mandatory spares you need to keep on board. I highly recommend the Racor brand, preferably those equipped with a water alarm system, as primary filters. These have a clear fuel bowl that lets you actually see water and/or contamination in the fuel. This is a major improvement over the solid metal filter housings that are typical as secondary filters with diesel engines.
Swapping out these fuel-filter elements is easy. You’ll need the correct size spanner wrench to loosen the single nut that holds the element into its housing. You’ll also need a drip pan to catch fuel that spills as you remove the filter housing assembly.
Make sure to replace the sealing gasket at the top of the filter housing assembly. Also make sure the new filter is a match for the one you are replacing. These are rated in micron size. Typical micron ratings are 5, 10 or 20, but they could be as small as 2 microns for the secondary filter.
Once reassembled, your filter assembly will be full of air. This is going to need to be bled out before running the engine.
2. Bleed the Fuel System
Air in your engine’s fuel system will occur when you replace your fuel filters, or if you run out of fuel in your tank. Either way, you are going to need to bleed the air out of your fuel system.
The method will vary depending upon the type of primary fuel pump. It gets the fuel from your tank to the engine.
If your boat has an electric pump, things will be easy. Simply crack open the fuel line that connects to the high-pressure injection pump on your engine, and then turn on the electric pump. Once you see fuel spitting out of the fuel-line connection, tighten the nut. Next, go to the engine’s fuel injectors and crack open the hex nut on the fuel line at the injector farthest from the injection pump. Tighten the connection when you see fuel spitting out of the line at the injector. Repeat this process on each fuel line, moving to the closest to the high-pressure injection pump.
If your engine has a mechanical primary fuel pump, then it will most likely have a small lever to let you activate the pump manually. Once all the air is bled out of the system, the engine should start up as normal.
One extremely important exception is if you have a newer electronic common rail injection system. Never, ever attempt to bleed these systems. They are self-bleeding, and they run at extremely high pressures that will cause personal injury if fuel sprays you.
3. Replace the Water-Pump Impeller
Add to your minimum spare parts list a raw-water pump impeller and cover gasket.
If you maintain your boat religiously, then you will rarely have to replace this impeller on an emergency basis. I replace the impeller on my boat every two boating seasons and have never had one fail. That said, it does happen, and replacement intervals will be dictated more by engine run time versus monthly intervals.
A clogged seawater strainer in the line that supplies water to the pump could cause an emergency failure. The impeller is made of rubber and is self-lubricated by this seawater. No water means no lubricant for the impeller, and premature failure will happen. It’s always best to follow your engine manufacturer’s recommendations as to service intervals.
To replace the impeller, remove the screws holding the pump housing cover. Typically, you’ll find a super-thin cover gasket. This will need to be replaced.
The rubber impeller can now be removed. Typically, prying it out with a pair of small screwdrivers will do the trick in sliding the rubber impeller off its driveshaft. A plethora of YouTube videos demonstrate how to service a raw-water pump. I recommend viewing several before you attempt this task.
4. Change the Engine Oil and Filter
Your engine manufacturer will specify change frequencies, along with oil type (American Petroleum Institute rating) and viscosity levels. It is imperative to use only the viscosity and API service rating recommended. Not all 30W oil is the same.
Even though your engine may have a conventional drain plug at the low point of the engine sump, in most marine installations, you won’t be able to access it effectively with a drain pan to catch the old oil as it drains out. So, the most common approach is to draw the old oil out of the engine through the dipstick hole. West Marine offers pump kits ranging from about $45 to $200, depending on how fancy you want to get.
Run your engine to warm things up before you begin the oil-change process. It’ll make things much easier because it will thin out the oil a bit.
Oil filters today are by and large of the spin-on variety. You might want to acquire an appropriately sized filter wrench to help with removal. Depending on the filter’s location on your engine, you might need a small catch basin to collect oil that leaks out as you remove the filter element.
Once it’s off, double-check to be certain that the gasket seal for the filter came off with the filter. The seal can stick on the engine. Remove it if it did remain in place.
Next, apply some oil on the gasket on the new filter, and screw it onto the engine. Hand-tighten only. Don’t ever use the filter wrench to tighten the new filter.
Next, insert the thin tube that came with the new oil-change pump into the dipstick hole on your engine until it bottoms out. Activate the pump (electric or manual), and suck the oil out of your engine.
Once all the old oil is removed, add the new oil in the amount specified in your engine manual. Start the engine, and look for any sign of leaking at the filter. Then shut down the engine and recheck the oil level.
5. Shut Down a Runaway Diesel
Although rare, having a “runaway” diesel is a terrifying experience for the uninitiated. You shut off all the engine controls, but your engine continues to run at full speed.
A number of things can cause this: excessive oil consumption that leads to oil accumulation in the combustion chamber, crankcase oil vapor entering the combustion chamber, turbocharger failure, damaged turbo seals, and fuel-system faults.
The good news is that all of this is unlikely on fairly new, well-maintained engines. But there are plenty of 20-year-old diesels in service today, and they are vulnerable.
Your diesel needs three things to run: air, fuel and compression. To stop a runaway, remove the easiest thing on that list to eliminate: air. Most diesels have some sort of an air breather protecting the air intake on the engine. It looks like an air cleaner on most engines but might not have a filter element installed. (Air filters are pretty useless at sea, where there’s not a lot of dust flying about.)
Keep a small block of wood on board that will give you a handhold, and block the air intake on the engine. Hold it in place, being careful to keep any and all body parts away from the air-intake hole. The suction will be extreme.
Expect the engine to continue running for a few minutes, depending on the size of the air-intake manifold. Eventually, the engine will smother itself and shut down. Then comes the hard work: finding the exact cause of the runaway.