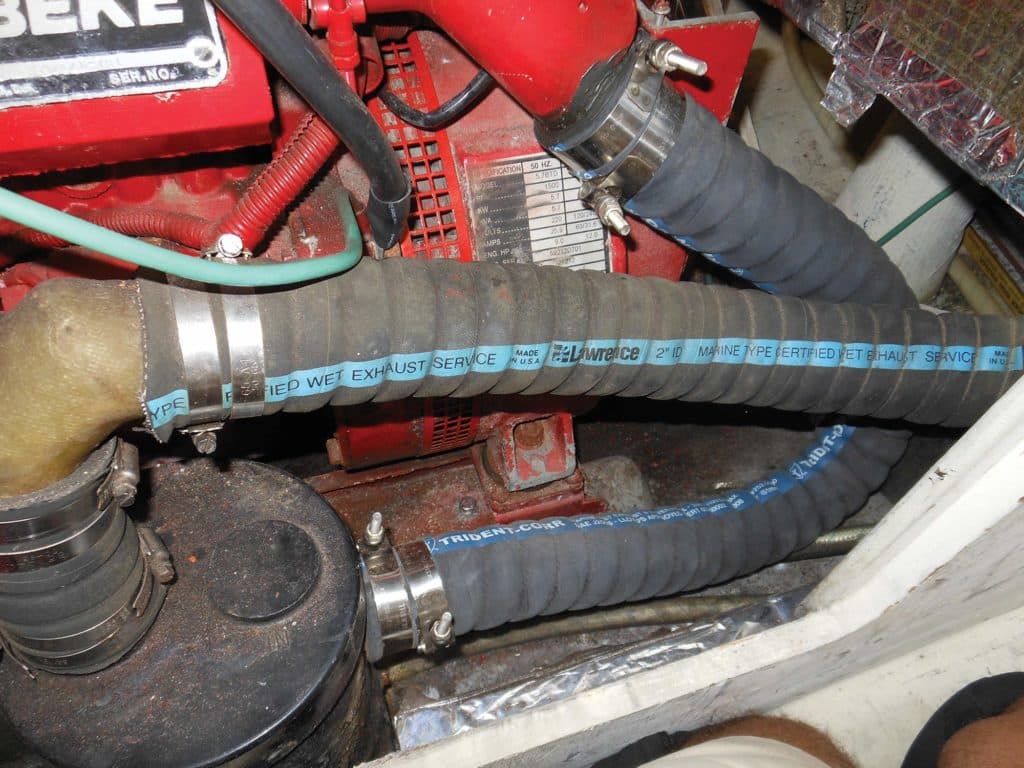
The requirements for designing a diesel-engine exhaust system are relatively simple, but when things go awry, they usually do so in a dramatic or expensive manner. Water ingress via the exhaust system is a common malady that affects auxiliary diesels, and it nearly always leads to significant damage, up to and including destroying an engine.
Fortunately, nearly all of these failure modes are well understood and easily avoidable with proper planning and material selection.
While engine manufacturers don’t supply complete exhaust systems, virtually every one that I’ve encountered clearly details the design requirements necessary to keep water on the correct side of the engine. Following these instructions is of paramount importance. Engine manufacturers do not warranty against water damage caused by ingress from the exhaust system.
Among other specifications, when inspecting your system, you should see a water-collection muffler, sometimes called a collector. Upon engine shutdown, water must never be trapped in the wet portion of an exhaust system, particularly between the exhaust mixing elbow (where dry exhaust and seawater mix) and the collector. If conditions are rough—and especially if the vessel is pitching heavily—water trapped in a section of hose could sluice its way into the exhaust manifold and then through an open exhaust valve into the cylinder.
Once water is there, the engine cannot be started. Attempting to start it can severely damage connecting rods and pistons. If the water is left there for any length of time, corrosion will set in, and the engine will likely seize.
RELATED: Troubleshoot an Overheating Engine
The solution? All the hose sections must be self-draining, with a minimum downward slope of no less than a quarter-inch per foot (about 1.2 degrees). Mufflers should be a minimum of 12 inches below the mixing elbow. These must drain to a water-collection muffler or overboard.
Water can potentially enter from two other locations. One is the exhaust discharge at the transom. This can be prevented by using a sufficiently high riser or gooseneck just forward of the transom, by installing a flapper on the discharge, or by using an internal check valve—in that order of preference. While a check valve might seem like the obvious solution, it has pitfalls, primarily the inability to see inside it.
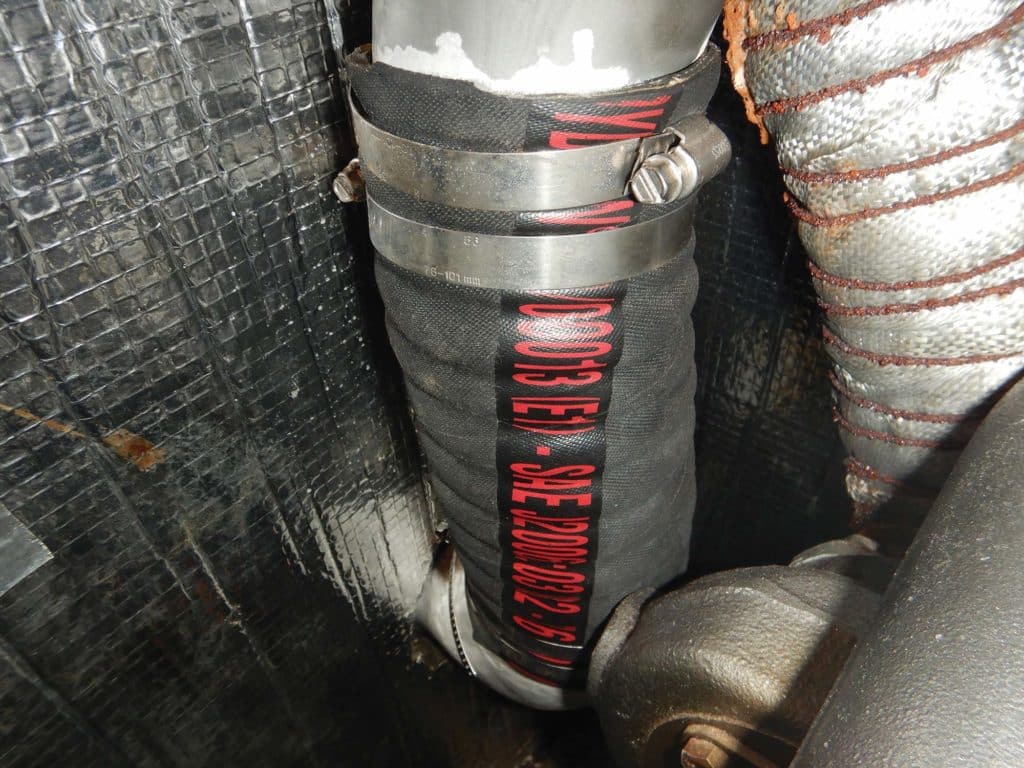
The other potential pain point is the raw-water supply to the engine. Raw-water plumbing must be equipped with an anti-siphon valve, which is installed between the heat exchanger and mixing elbow (on the pressurized side of the raw-water system). Anti-siphon valves are simple devices, but they can fail, they can clog, and they can be installed incorrectly. Make certain yours is high enough above the dynamic line, at all anticipated angles of heel while motorsailing, to ensure that it will open. The general rule is for anti-siphon valves to be placed no less than 12 inches above the dynamic waterline. Higher is better. Valves should be inspected and cleaned annually.
“But it’s been this way since I bought the boat, and it’s never been a problem. Why should I change it now?” is a refrain I often hear after pointing out a design flaw in an exhaust system.
And yet, I’ve also encountered cases where engines have flooded with seawater after years of use. The mechanical stars aligned, enough water accumulated in a hose, and the vessel slid down a wave, shuddering to a halt when entering the trough, forcing water just far enough up the exhaust and through the elbow.
If your exhaust system doesn’t meet the engine manufacturer’s specifications, it’s never too late to correct it. Doing so might save you untold grief and expense.
Steve D’Antonio offers services for boat owners and buyers through Steve D’Antonio Marine.