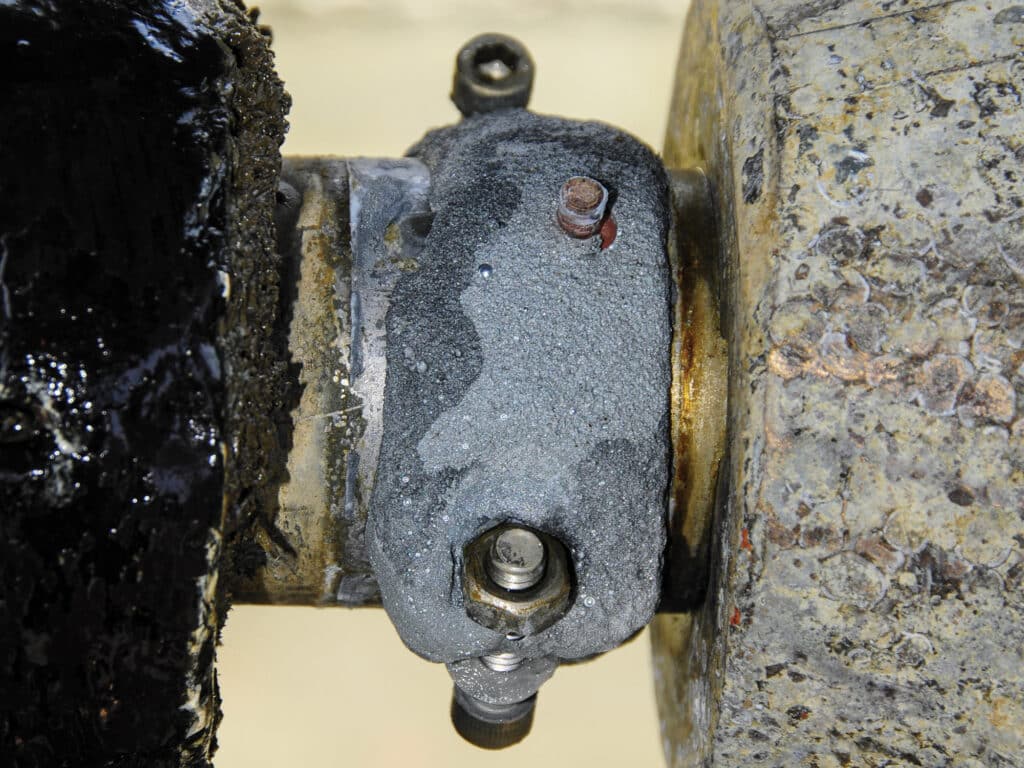
Not long ago, I saw a boater write online: “My vessel has no bonding system, and everything seems to be fine. Do I need one?”
It’s a great question. Like so many things electrical, you can’t actually see what’s happening—or not happening—with a bonding system, making it tempting to draw conclusions that are often incorrect.
Let’s begin with terminology. The words “bonding” and “grounding” are often used interchangeably. For the purposes of this column, we’ll look at bonding systems specifically.
Cathodic protection refers to the utilization of a system that relies on a sacrificial metal, the anode, to protect underwater metals, or cathodes.
Anode refers to a sacrificial metal, often zinc, although it can be aluminum or magnesium. Zinc is suited for seawater applications; aluminum is appropriate for seawater, brackish water or fresh water; and magnesium can be used only in fresh water.
The primary goal of a bonding system is to electrically connect disparate, submerged metals, usually via wire (American Boat and Yacht Council standards call for a minimum of 8-gauge tinned cable). An anode is then connected to the bonding system, providing cathodic protection to those same interconnected metals. As long as the anode is maintained, and the resistance between the anode and any connected metal is kept below 1 ohm, then galvanic (dissimilar metal) corrosion can be avoided.
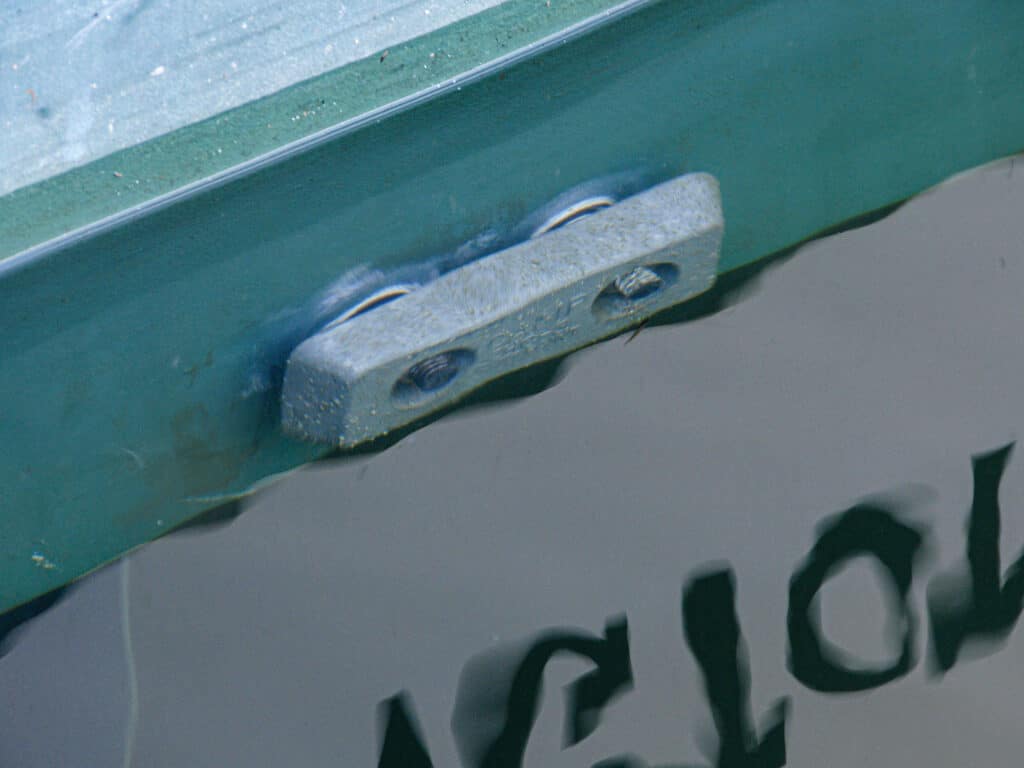
While galvanic corrosion is a slow process, occurring over months or years, stray-current corrosion can lay waste to underwater metals in a matter of days. In severe cases, it can lead to flooding and sinking.
Stray-current corrosion occurs when DC battery current leaks into bilge water or the water around the vessel, usually via a damaged wire or other exposed connection in the bilge. While it’s not guaranteed, a bonding system can help stem the effects of stray-current corrosion. It provides a more direct, lower-resistance path back to the source—the vessel’s battery
—rather than through the water. With that low-resistance return path, the likelihood increases of a fuse blowing or circuit breaker tripping. That’s good because it stops the harmful current flow.
When current flows through water, some metal will almost surely come to grief. In their benevolent form, sacrificial anodes are consumed via the cathodic-protection process. These anodes should be replaced when they are no more than 50 percent depleted. Through-hulls, struts and other underwater metals may fall victim to stray-current corrosion. (Anodes, by the way, can stave off only galvanic corrosion; they are no match for stray-current corrosion, which will consume them in short order.)
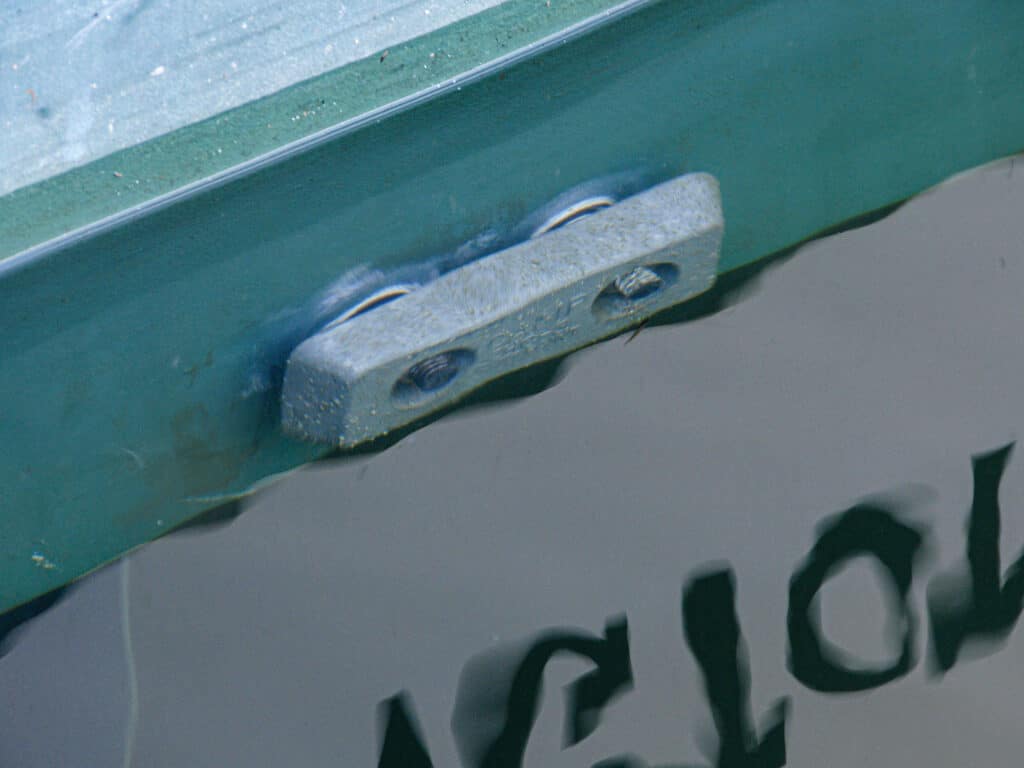
Bonding systems protect submerged metals, seacocks, shaft logs, rudders and the like. Other metal objects inside the vessel, including the engine and generator, even if bonded, will be afforded no protection from corrosion because they are not immersed in the same body of water as the hull anode. (Engines should be bonded only if they utilize isolated ground starters and alternators.) In order for cathodic protection to work, the protected metal and the anode must reside in the same water, and the interconnection between them must be of very low resistance. Engines and generators must rely on either their own anodes or, in some cases, alloys that manufacturers believe do not require cathodic protection.
Shafts and props—because they are often only tenuously connected to the bonding system via the marine gear, which is oil-filled—cannot rely on hull-mounted anodes for cathodic protection. They must utilize their own anodes. The average, inexpensive shaft brush is incapable of meeting the 1-ohm resistance standard.
Steve D’Antonio offers services for boat owners and buyers through Steve D’Antonio Marine Consulting.