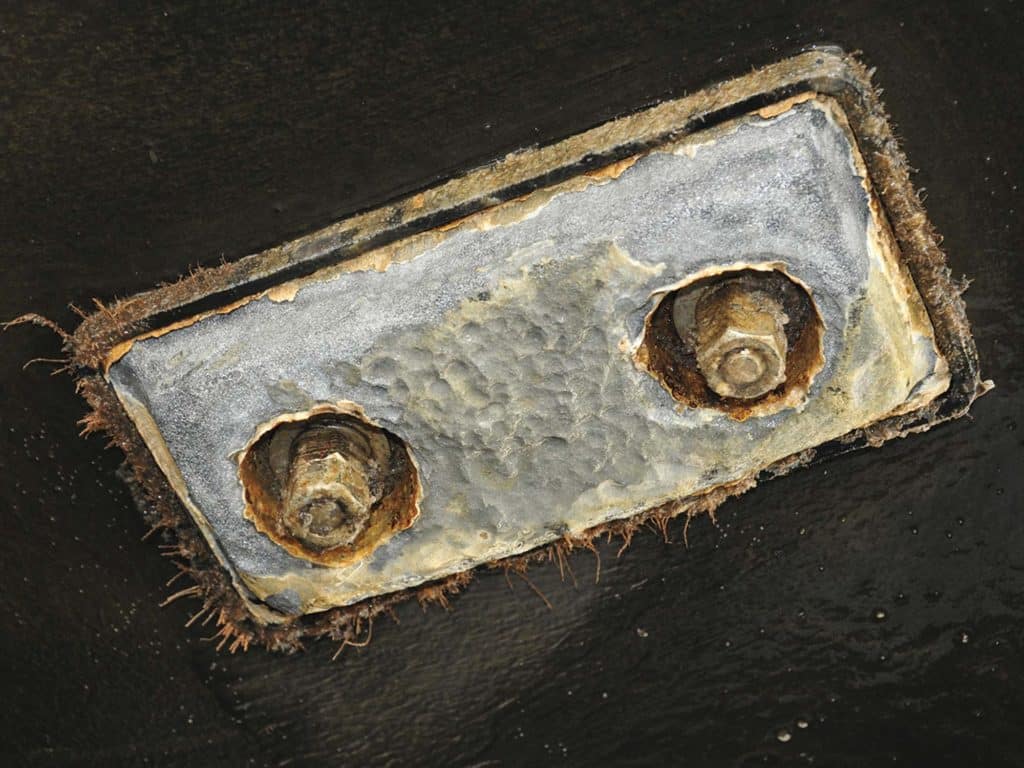
Halos in bottom paint around underwater hardware is a phenomenon I encounter on a regular basis. And just as often, I’m asked: “What causes this? Is it something to worry about?” The answers lie in an understanding of underwater metals and bonding systems.
Most fiberglass sailing vessels rely on metal alloys for through-hull fittings, struts, rudder gudgeons, hinges and so forth. In most cases, these metals are connected by wires (part of the vessel’s bonding system) to a sacrificial anode or anodes, which provide what is commonly referred to as cathodic protection.
From a corrosion perspective, the anode—often called a “zinc,” even though it can be zinc, aluminum or magnesium—is less noble, and thus more prone to corrosion, than the metals to which it is connected. As a result, the anode corrodes, or sacrifices itself, in order to protect the other metals.
A well-maintained anode should be replaced when it’s no more than 50 percent depleted, to provide adequate protection for other submerged metals. How do you know if the anode is depleted? The corrosion process is galvanic-electric, which means that interconnected, dissimilar metals immersed in an electrolyte (seawater, in this case) will reach a negative voltage. That voltage can be measured using a reference cell.
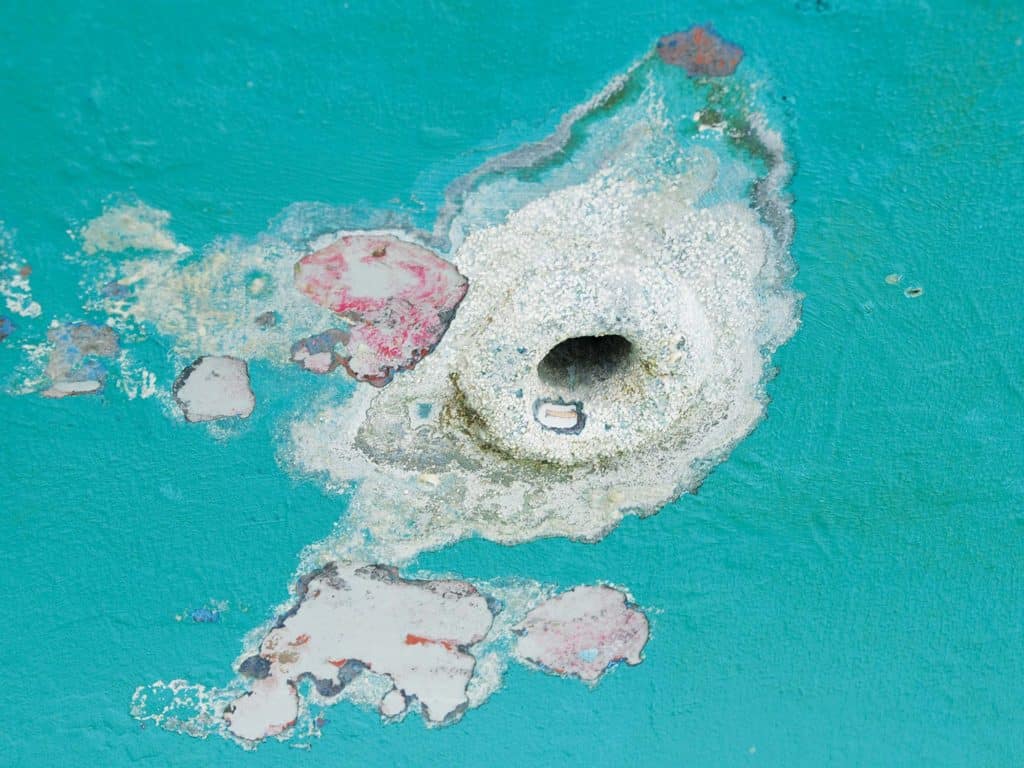
Too Much of a Good Thing
The needed volume, surface area, and weight of anodes is a function of several factors, including the surface area of the metals being protected, water salinity, temperature, and movement. The goal is to use enough anodes to drive each metal to a minimum of 200 mV more negative than its resting voltage, which affords it the necessary protection; for fiberglass vessels, this is usually about negative 550 to negative 1100 mV. That approach, along with maintaining the bonding system to ensure that no more than 1 ohm of resistance exists between protected metals and anodes, will keep galvanic corrosion at bay. All of this might lead boaters to conclude that if some zinc is good, more is better. There is some truth to this. However, there can be deleterious side effects from overprotection, which produces an alkaline solution around the protected metals (there can also be an interaction with the copper in many bottom paints). In the case of fiberglass vessels, this situation can lead to paint failure, called cathodic disbondment—the familiar haloing. The loss of antifouling paint then often leads to the formation of marine fouling. Overprotection is not harmful to bronze or stainless steel. It can be prevented by reducing the number of anodes, or by epoxy-coating these metals to encapsulate them, to stop the formation of alkaline.
At the same time, overprotection can be destructive to boats made of wood or aluminum. The soft pulp between wood’s grain, called lignin, is dissolved by alkaline, leading to a phenomenon known as delignification, which will compromise the wood’s strength. Aluminum is an amphoteric metal, which means it can be attacked by an acid or an alkaline solution.
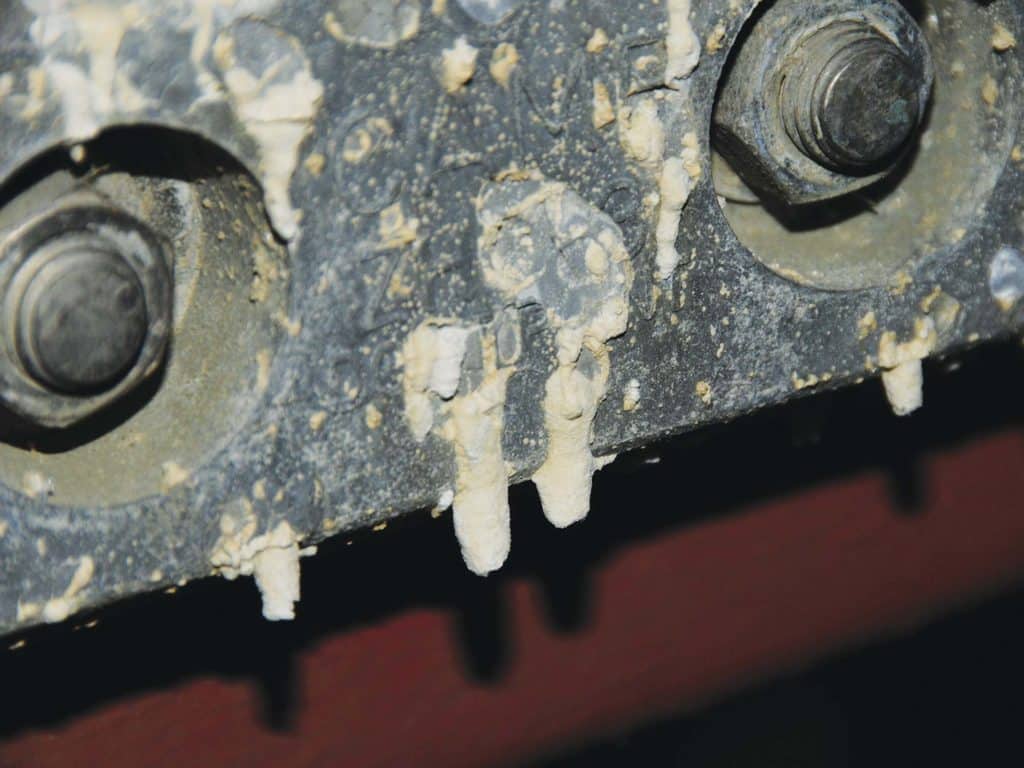
Ultimately, no matter the type of boat, try to provide the right amount of cathodic protection, especially in the case of wood and aluminum hulls.
Steve D’Antonio offers services for boat owners and buyers through Steve D’Antonio Marine Consulting.