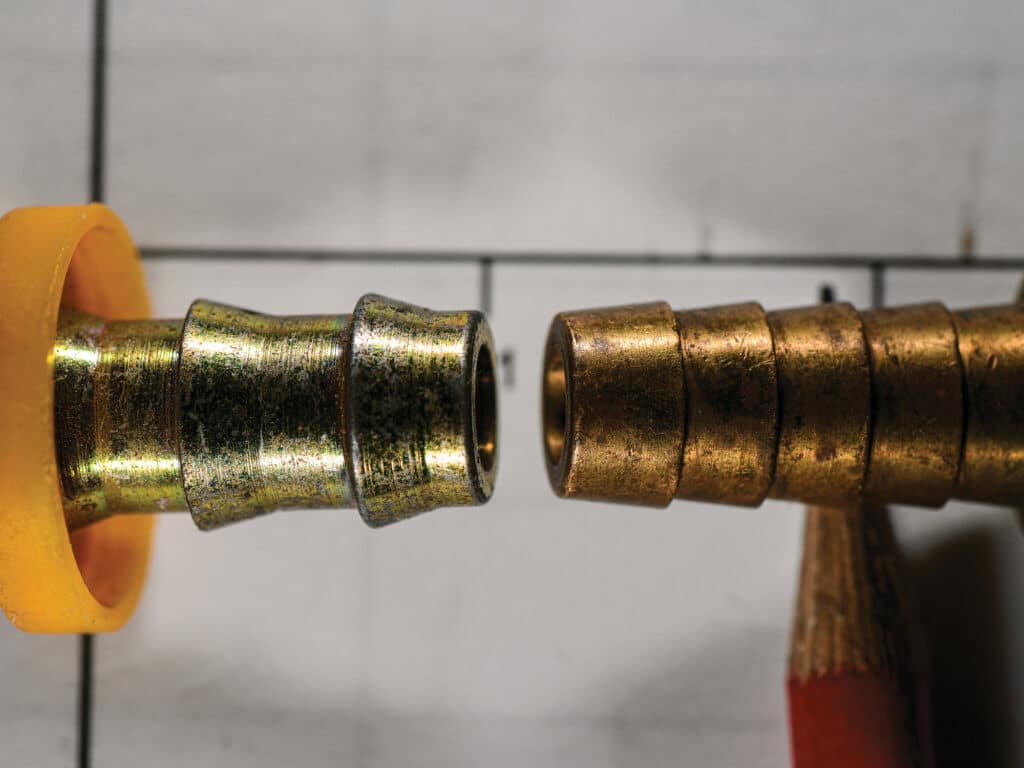
Since their advent in the early 20th century, diesel engines have been refined to a state of near perfection. Most are robust, reliable and long-lived, provided they receive preventive maintenance, clean fuel, cooling water, and air for combustion.
When they do fail, the problem can usually be traced to a handful of culprits: deferred maintenance (a deteriorated impeller or broken belt, for instance) or contaminated or interrupted fuel, with the latter including air ingestion, an electrical fault, or a design or manufacturing defect.
This column focuses on fuel plumbing. Fuel is usually conveyed from the tank to the engine via flexible hose; in some cases, it’s via copper tubing. Any hose that’s used must be rated for marine fuel applications, including the ability to resist exposure to flame for a minimum of 2.5 minutes. Hose that meets this requirement is typically marked USCG A1. It should also include the name of the manufacturer, as well as the date it was manufactured. If any of this information is absent, particularly the A1 rating, then the hose is disqualified for use in a marine fuel application.
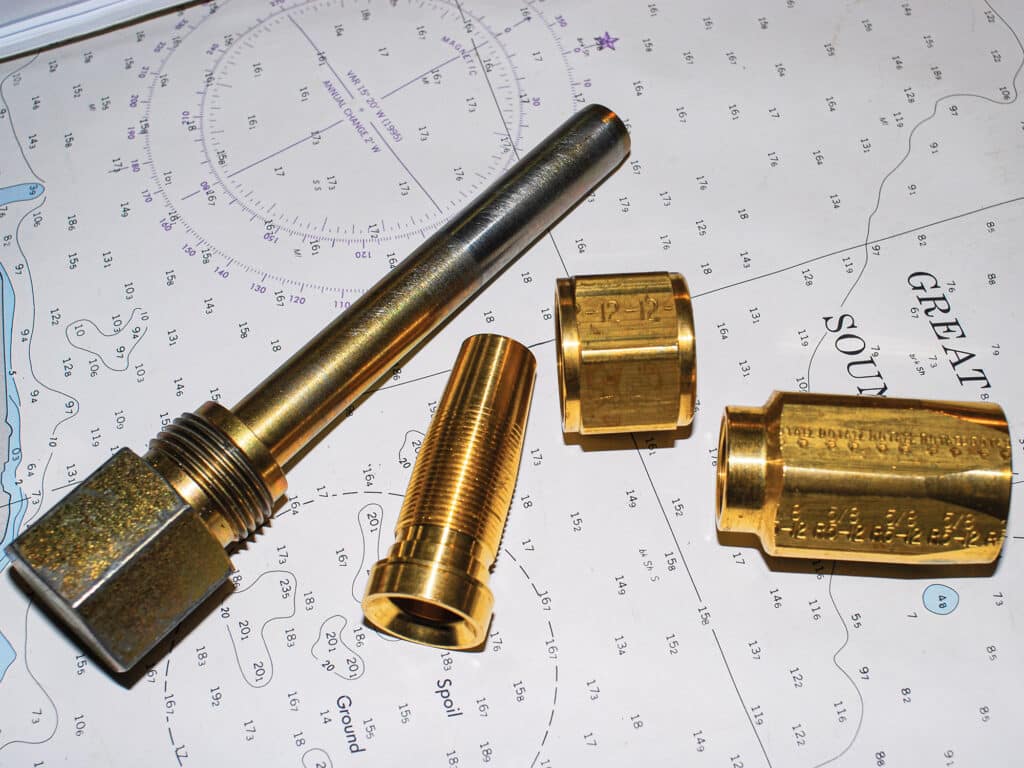
A section of flexible hose must be used between the tubing and the engine, and the tubing must be immobilized against engine vibration and gear shifting. For this transition location from metallic tube to hose, the interface cannot be direct. Put another way, the hose cannot simply be clamped over the tube. The tube must instead be flared, and a flare-to-hose fitting should be used.
Termination of fuel hoses is most often achieved by using common pipe-to-hose adapters and hose clamps. While welcomed, double clamps are not required, at least where American Boat and Yacht Council compliance is concerned.
In fuel-supply applications, double clamps should be used only if the adapter is long enough to support both clamps with room to spare. If the adapter is not long enough to support dual clamps, then a single (preferably solid rather than perforated) band clamp should be used.
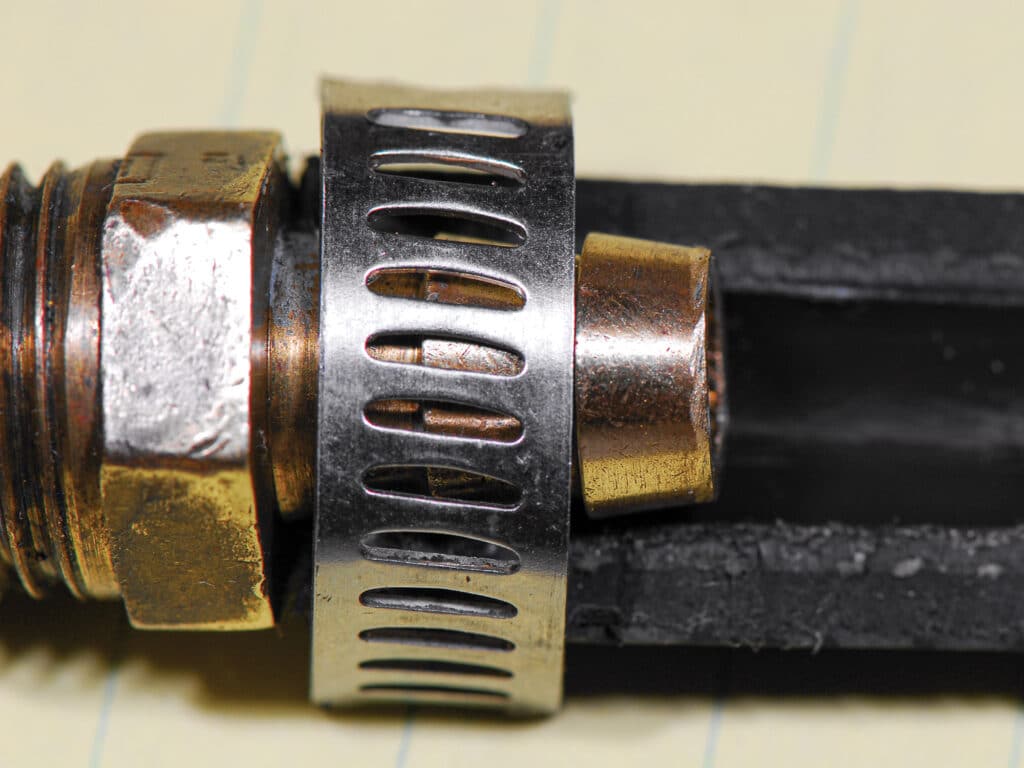
One caveat where this practice is concerned: Some adapters are designed to be used without clamps. They are often differentiated from conventional adapters by a plastic collar. The barbs on these adapters are especially aggressive; if clamped, they can pierce the hose’s inner liner, leading to leaks and delamination, and interrupting the fuel supply. And these adapters can be used only with hose designed and labeled for the application.
The other form of hose termination utilizes a clamped or swaged in-place fitting. Clamped or field-assembled fittings are available in brass and plated mild steel. Brass fittings are reasonably priced and corrosion-resistant. Mild-steel fittings are cost-effective but should be corrosion-inhibited after they are installed. When installing these fittings, a proprietary installation mandrel must be used to prevent damage to the hose liner, which could ultimately create a blockage.
Swaged fittings require the use of a swaging tool, and thus are poorly suited for do-it-yourself projects. If you know the lengths you need and the end-fitting types, you can have a batch of hoses swaged by a commercial hose shop.
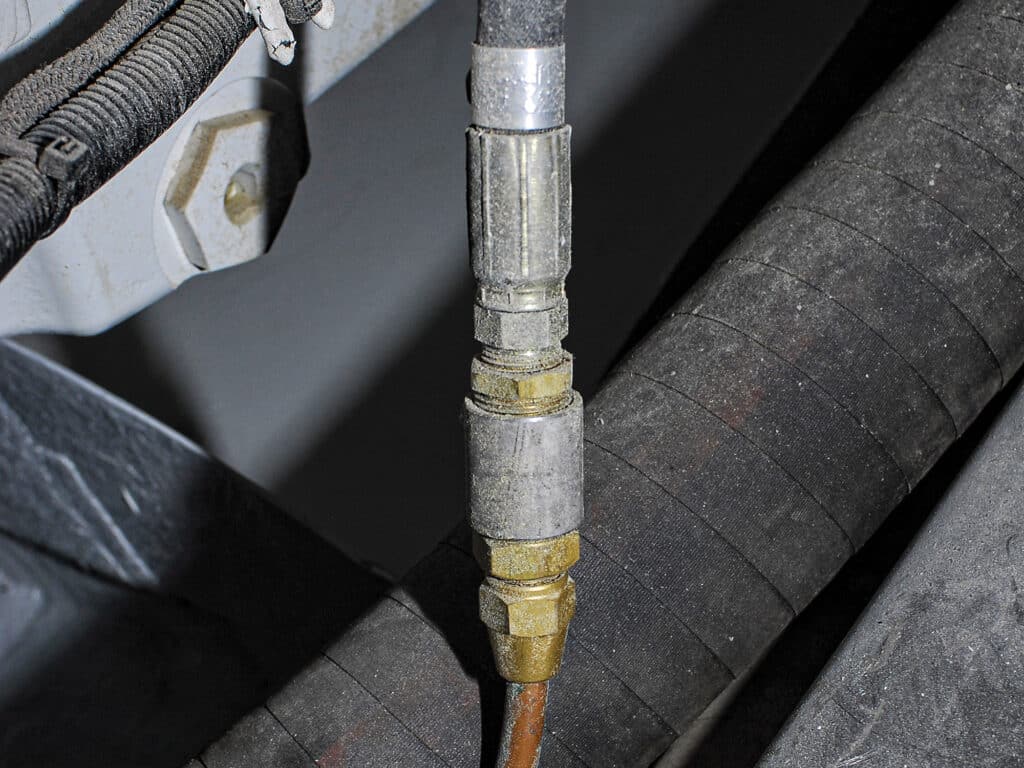
Fuel-fill hose must also be rated and marked for the application. It calls for an A2 rating. In this case, double clamps are not only recommended, but they are required for ABYC compliance. This is one of only two applications where double clamps are mandated, with the other being exhaust hose.
Steve D’Antonio offers services for boat owners and buyers through Steve D’Antonio Marine Consulting.