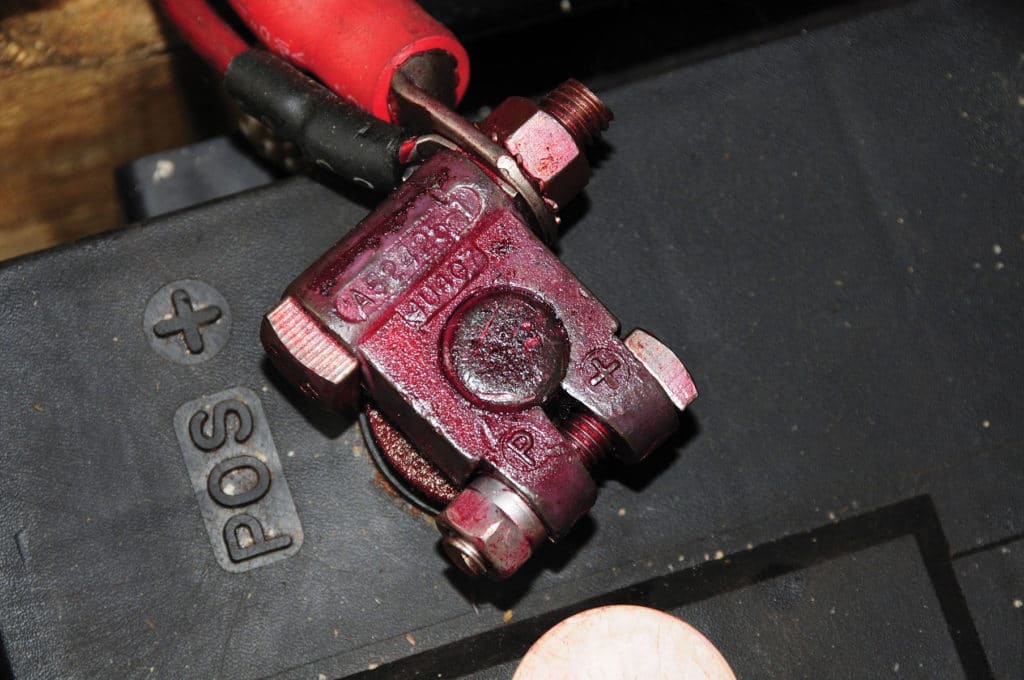
Battery-Post Adapter Terminal
There are numerous ways to connect battery cables with battery banks. Even if your boat’s battery banks and DC electrical system are well designed and robust, if the interface between the two is tenuous, then reliability will suffer.
Different types of battery posts — the metal portion that’s an integral part of the battery — often dictate the connection method. Cylindrical lead automotive-style posts are common. These require an adapter to attach to a cable’s ring terminal, a necessary evil: Inserting anything between the cable and the battery introduces the potential for increased resistance, arcing, heat generation and failure. Also, ignition sources adjacent to batteries, such as sparks, can lead to a hydrogen explosion, especially if the batteries are flooded. So it’s imperative that battery connections are secure and maintain a low resistance path for current flow.
There are several types of automotive post adapters;the best rely on fastener copression to maintain electrical and physical integrity. The so-called “military battery terminal” is one example. Tightening the clamping and electrical-connection fasteners of this terminal compresses the assembly, enhancing its security. A more common, less reliable arrangement relies on a stud that is cast into the terminal’s comparatively soft lead structure. This design may fail when stressed by stiff, heavy or multiple battery cables, or if the terminal overheats.
Batteries that are designed for marine and industrial applications are often equipped with flag terminals — bladelike protrusions that take the place of an automotive post. These may be copper, and usually are found on AGM (lead-acid) batteries. A hole in the flag enables a ring
terminal to be through-bolted directly, without an adapter. With AGM or gel-cell batteries, over-stressing the flag with stiff or poorly supported cables can lead to case leakage, which will shorten the battery life.
A threaded post terminal vaguely resembles the automotive post. However, it’s often made of copper alloy rather than lead, and it includes a vertical thread and fastener, which allows direct ring-terminal attachment.
For all terminals, following a few guidelines will increase reliability and reduce the likelihood of arcing and fire or explosion. The hole in the ring terminal must match the size of the fastener to which it’s secured, without washers. And washers must never be placed in the current path between a cable’s ring terminal and the battery terminal.
Washers, especially stainless-steel ones, present comparatively high resistance to current flow, which leads to heating and expansion, and ultimately loose connections. It’s not unusual to find washers installed in this manner that have turned purple from extreme heating.
ABYC guidelines limit to four the number of ring terminals that may be placed on a single stud; I prefer no more than two. More connections on a single post increase the potential of resistance, particularly in this corrosionprone environment. Installing a bus bar adjacent to the battery is one way to reduce the number of connections at a given post or terminal. Make certain positive terminals and bus bars are fully insulated to prevent short circuits. Finally, using a conductive paste such as Thomas & Betts Kopr-Shield at the interface between the various connections makes excellent sense, as it excludes air and moisture, reducing the likelihood of corrosion. Once connections are completed, spray them with a protective coating such as CRC Battery Terminal Protector to further enhance reliability and safety.
Steve D’Antonio offers services for boat owners and boat buyers through his company, Steve D’Antonio Marine Consulting.