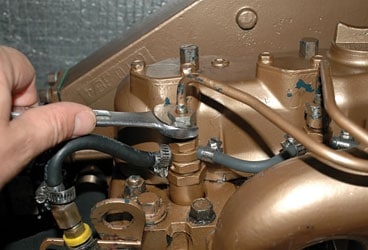
A few years ago, I received a call from a customer who was cruising (or not cruising, as it turned out) in the Bahamas aboard his 45-footer. Both his engine and generator had shut down simultaneously, he couldn’t get his anchor to set securely, and he was being blown onto a lee shore. With spotty satellite-phone coverage, it took several calls before I learned that after experiencing a loss of power, he’d replaced the primary and secondary fuel filters on both the engine and the genset, and in doing so, air had entered the high-pressure fuel system of both engines. The solution seemed simple: Bleed both engines-the propulsion engine first, of course-and be on your way.
The problem was that neither he nor his crew had ever bled an engine before. A few calls later, I’d walked him through the process, and he’d learned an important lesson: Know how to bleed your engine’s diesel system, or suffer the consequences.
While the actual procedure for bleeding a fuel system varies from engine manufacturer to engine manufacturer, the basics are pretty much the same. If your engine has a mechanical-lift fuel pump-this is the low-pressure pump that’s attached to the engine-it will often be equipped with a small lever that lets you pump fuel without turning on the engine. To purge air from the low-pressure side of the fuel system, open fuel-line unions and bleed ports downstream of the pump, one at a time, beginning with those closest to the pump, and continue pumping until fuel, and not air, runs out. The procedure for engines equipped with electric fuel pumps is similar, but instead of working a lever, you turn the ignition key to the on position to activate the pump. On some engines, the electric pump only runs when the glow plugs are operated or when the engine is actually running, so in this case the pump may have to be temporarily hot-wired.
The fuel system’s secondary or on-engine fuel filter is located between the lift pump and the high-pressure injection pump, and it’s here that air often becomes trapped. Most secondary fuel filters are equipped with a bleed screw. Opening this and working the lift-pump lever until a clear stream of fuel flows out means that you’ve successfully bled the system up to that point.
Next comes the injection pump. Most are equipped with bleed screws, and thus the procedure is the same. Then you must bleed the high-pressure fuel system, which is done by loosening the union nuts between the top of the fuel injectors and the fuel line; it just takes a turn or two. Once loosened, use the starter to crank the engine for 10 seconds. If fuel fails to make an appearance at the unions, wait 60 seconds (to allow the starter to cool), then crank again for 10 seconds. The process could require several repetitions until fuel dribbles out. When it does, tighten the unions and crank the engine with the throttle advanced 25 percent. It should catch, although it may run rough at first. Advance or retard the throttle until the engine begins to run smoothly.
A note of caution is in order here: If you must crank the engine for more than about 20 seconds, close the cooling-water intake seacock. Each time the engine is cranked, it pumps water into the exhaust system, and until the engine starts, the water will accumulate there. Eventually, it can reach the exhaust manifold, exhaust valves, and ultimately the cylinders, causing extensive damage. Remember, however, to open the seacock once the engine begins to run.
Steve D’Antonio is a regular Cruising World contributor who offers services for vessel owners, boatbuilders, and others in the marine industry through Steve D’Antonio Marine Consulting.