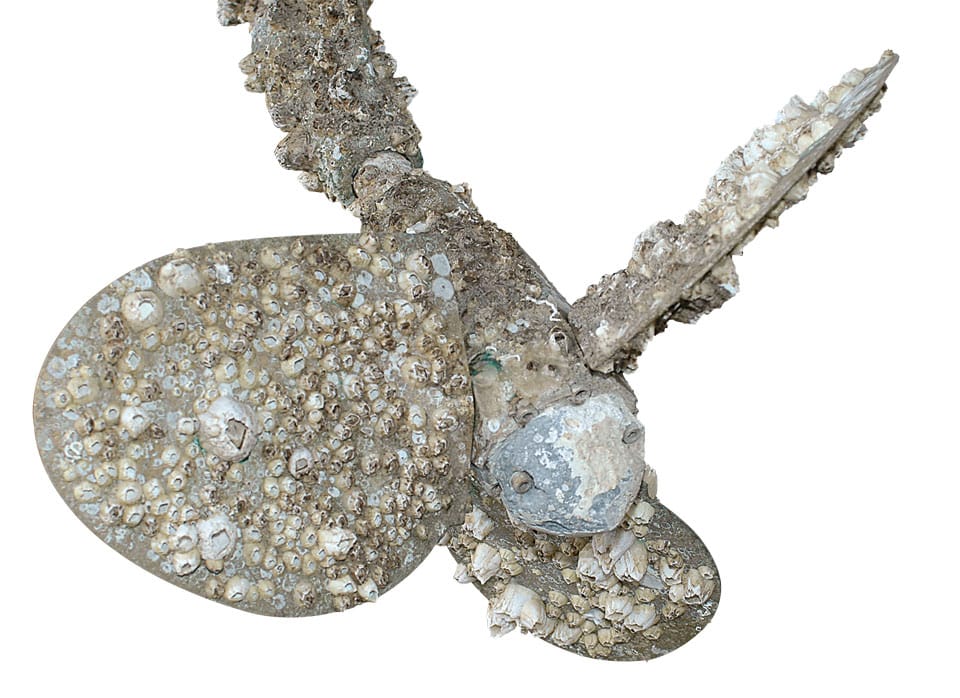
Propeller
Keeping the propeller and shaft from becoming encrusted with hard marine growth is an age-old challenge. If you cruise in an area where such growth is pervasive, it makes sense to consider a strategy more proactive than a mask, fins and a scraper.
A vessel’s propeller and shaft, or running gear, works best when it’s clean and free of barnacles. As with the bottom, if barnacles and other marine organisms are allowed to strike on these surfaces, efficiency and performance drop while fuel consumption increases. Overheating or incipient engine damage may also occur.
Fouled running gear can also jeopardize a diesel engine by causing fuel overload, when more fuel is delivered to the cylinders than can be burned. This can lead to the production of black smoke (a result of incomplete combustion), localized internal overheating, soot accumulation, clogged piston rings and valves, and other issues.
The solution seems simple: Treat the running gear like the bottom, with a good coat of antifouling paint. Regrettably, it’s not that easy. Most conventional antifouling paints simply won’t adhere well — if at all — to such otherwise untreated metal components as propellers, shafts and, to a lesser degree, struts. It’s imperative to make sure that these items remain free of growth. Once fouled, they create drag and upset the clean flow of undisturbed water into the propeller, which once again compromises its efficiency.
There are several ways to address this problem. First, you can apply an epoxy primer that acts as a “tie coat” between the bare metal and the antifouling paint. Epoxies adhere tenaciously to most surfaces and are able to bond chemically with subsequent applications of compatible antifouling paint; the epoxy develops a mechanical bond with a properly profiled metal surface, and the antifouling paint establishes a chemical bond with the epoxy primer.
In order for each of these bonds to succeed, application instructions from the manufacturer must be closely followed. Use light media blasting or sandpaper to abrade, or profile, the running-gear surface, then thoroughly degrease or remove surface-oil contamination. This gives the epoxy a toehold on an otherwise slick surface. The chemical bond, on the other hand, calls for compatibility between the primer and the antifouling paint; ideally, they should come from the same manufacturer, and the paint should be hard, rather than ablative, so it won’t wash off in the turbulence surrounding a prop and shaft.
Application of the primer and the antifoulant must follow established time windows to ensure the formation of the all-important chemical bond. If the windows are missed, the bond between antifoulant and primer will be tenuous at best. It’s important to remember that ambient temperature affects these windows; they narrow as the temperature rises. Most of the failures in such antifouling applications are a result of poor adherence to chemical-application windows.
You can also try proprietary antifouling paint intended for running gear. These package products provide the necessary cleaner, primer and antifoulant in one kit. However, the importance of preparing surfaces properly, following application instructions and working within the required application windows remains the same. Skip or ignore any of these steps and your hard work will be for naught.