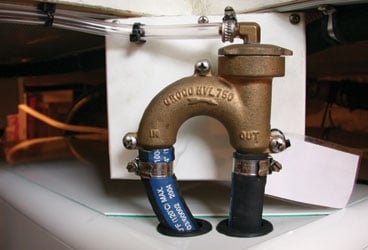
anti siphon valve 368
I first saw a siphon in action when I was a small boy. A neighbor used one to get water out of a boat that was stored on land. I watched as he filled the hose with water, put one end in the boat, and held his thumb over the other end as he lowered it to the ground. When he removed his thumb, the water in the hose drained, beginning the siphon, which continued to flow until the boat was empty. It seemed like magic.
Now I know that siphons can also lead to flooding and even sinking. And that’s why the anti-siphon valves on your sailboat are vital pieces of equipment. Without them, raw-water siphons may develop in several areas aboard a vessel: in the engine and the generator, in the head, and in the bilge via bilge pumps.
If your engine is installed at or below the waterline, then a siphon may develop when water being drawn in for cooling continues to flow after the engine is shut down. If this happens, seawater will flow into the exhaust as it does while the engine is running; however, without exhaust gasses to expel it, it will eventually fill the muffler, then the hoses, and eventually the engine itself. Under the right circumstances, water may then leak into the boat, eventually causing it to sink. I’ve seen this exact scenario transpire over the course of just a day or two.
In the head, the bowls of many marine toilets are lower than the intake opening, and seawater may continue to flow after a head has been flushed, especially if pump valves haven’t been properly closed. In both examples, the insidiousness of the problem lies in the fact that the siphoning may not happen for years, as long as the engine’s impeller and the rubber flapper valves in the toilet remain in good condition. Once those parts become damaged or worn, then a siphon is free to occur.
For bilge pumps, the problem is exceedingly simple: Siphons begin while the boat is under sail when the discharge is submerged, despite the fact that the discharge hose rises at some point above the heeled waterline. When a pump cycles off, the water running back into the bilge initiates a self-sustaining siphon.
Every engine, head, and bilge pump needs a properly installed anti-siphon valve, sometimes also called a siphon break or a vented loop. In an engine room, anti-siphon valves are typically installed between the heat exchanger and the injection point on the exhaust elbow; in the head, between the raw-water flush pump and the bowl (they’re commonly and incorrectly installed on the pump-inlet hose); and anywhere along the discharge line for the bilge pump. The most important aspect of the installation is that the valve remains well above the waterline under all operating conditions and on all points of sail. To ensure proper operation, some manufacturers of anti-siphon valves require the valve to be installed a minimum of 2 feet above the dynamic waterline.
These valves should be inspected monthly and serviced, disassembled, and cleaned seasonally to prevent clogging. If you’re not sure if a hose needs an anti-siphon valve, then install one. There’s little harm in having one where it’s not needed; however, untold difficulty and damage may occur when one that’s needed hasn’t been put in.
Steve D’Antonio, a regular CW contributor, offers services for vessel owners, boatbuilders, and others in the marine industry through Steve D’Antonio Marine Consulting. Next month, he writes about the maintenance required to keep seacocks working smoothly.