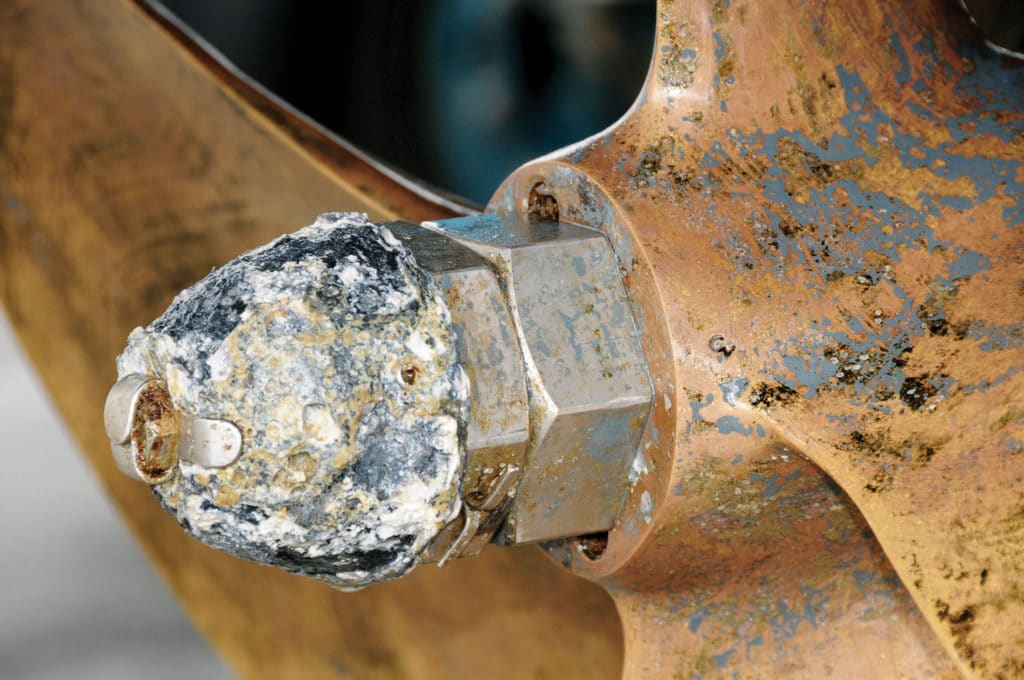
Prop Needs Own Anode Protection
Recently, I received a note from a client that captures the often misunderstood role of, and science behind, sacrificial anodes: “I’m afraid to change the type of zinc I use. Mine seems to work and lasts a long time. My diver told me that aluminum zincs don’t work anyway.”
While commonly referred to simply as “zincs,” sacrificial anodes are in fact available in several different alloys including aluminum, magnesium and zinc, although the latter is the most common. (All anodes contain alloying and trace elements of other metals.) In fact, each metal is best suited to a different environment. Traditionally, fiberglass vessels operating in seawater employ anodes made from a zinc alloy; although ubiquitous, however, they are not necessarily the most desirable option.
Sacrificial anodes are used for one purpose: to prevent or deter corrosion of underwater metals such as propellers, bronze through-hull fittings, and stainless-steel propeller shafts and rudderstocks. (Once again contrary to popular belief, most props are made of a brass alloy such as manganese bronze, which contains zinc and is particularly susceptible to corrosion if not protected by an anode.) Each of these metals should be protected by a sacrificial anode, either directly or indirectly through the vessel’s bonding system.
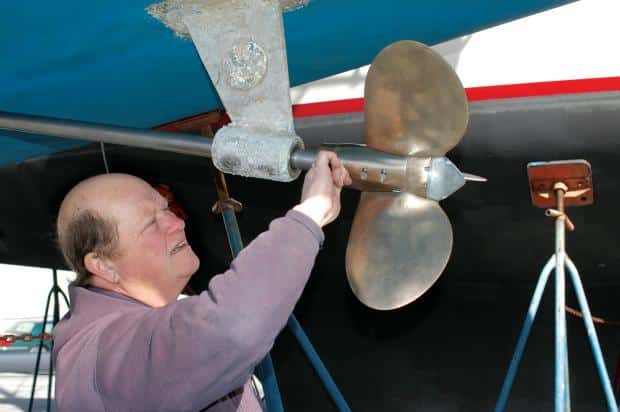
| |Anodes for folding and feathering props are often hard to find, so keep spares aboard.|
Regarding galvanic corrosion, each metal possesses its own natural corrosion potential, measured in millivolts: the more “negative” they are, the more prone to corrosion. The goal of the anode, then, is always to be more negative than the metal it’s protecting. The relative energy capacity of zinc is 368 amp hours per pound with a voltage of negative 1,050 millivolts. While that’s adequate in most cases, zinc anodes possess one flaw: When used in brackish or fresh water they are prone to developing a calcareous coating, a whitish material that essentially puts a zinc anode to sleep. Many sailors mistakenly perceive these especially “long-lived” zincs as effective. In reality, they’re anything but; even where anodes are still present, they provide no anodic protection at all. An anode that lasts for an inordinately long time probably isn’t working for any number of reasons, calcareous coating or otherwise.
Aluminum anodes, alternatively, offer several advantages. They’re immune to the calcareous coating menace and are therefore well suited for use in seawater, as well as brackish and fresh water. Aluminum anodes also pack more of a punch; they either last longer than zinc anodes of the same weight, or provide the same protection as zinc in a lighter package. Their relative energy capacity is 1,108 amp hours per pound (significantly more than zinc), with a voltage of negative 1,100 millivolts. If you opt for aluminum anodes, be sure that the change is universal for all anodes used within the same bonding system.
Surprisingly, aluminum anodes are often no more costly than zinc ones. Also, because most are cadmium-free, aluminum anodes are less of a hazard to the marine environment. So, regardless of what a diver, boatyard manager or other industry pro tells you, there are several advantages, and no drawbacks, to switching to aluminum anodes.
As for magnesium anodes, these work in fresh water only. Don’t use them if operating your boat in the briny.
Finally, when purchasing anodes, select those that meet stringent military specification standards: A-24779, A-18001 or A-21412 (for aluminum, zinc and magnesium, respectively). These standards ensure the purity of the alloy, an important factor in an anode’s effectiveness, resistance to self-fouling and longevity. Inexpensive anodes often represent false economy.
_Steve D’Antonio offers services for boat owners and boat buyers through his company, Steve D’Antonio Marine Consulting. This article first appeared in the January 2014 issue of Cruising World.
_