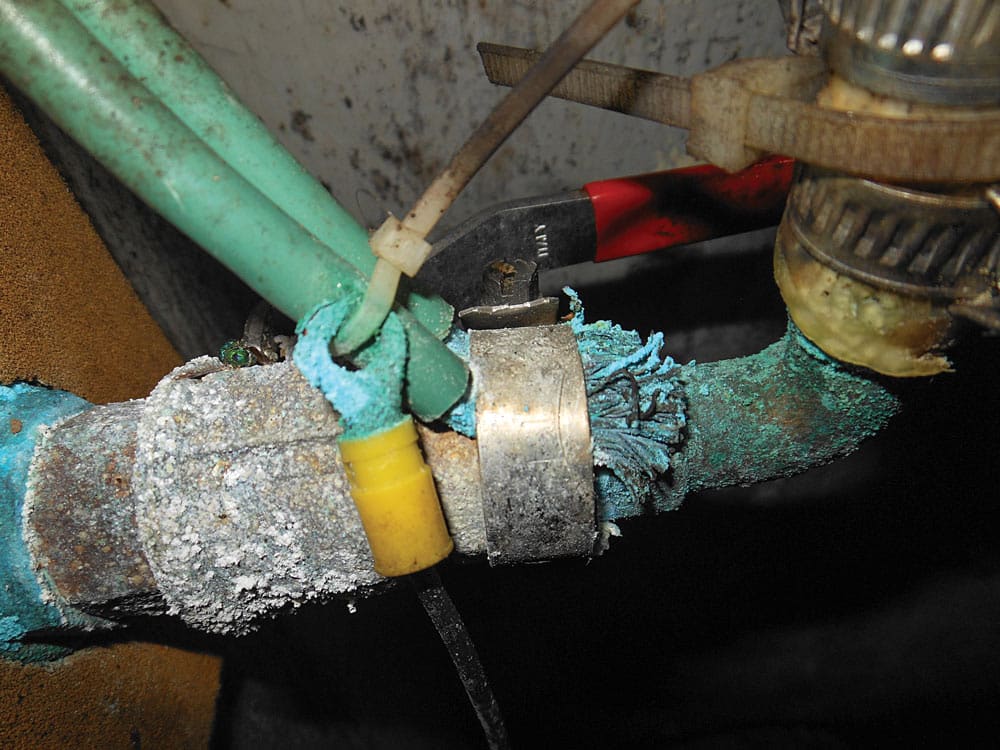
Corrosion
Inescapable and ever present, corrosion remains among the most misunderstood of all onboard phenomena. And no wonder; sailboats are built using a wide range of metallic components, from bronze seacocks and iron engine blocks to stainless-steel and aluminum deck hardware and copper wiring. Add water to this mix, especially seawater — or electricity — and the results can be heart-achingly unpleasant and jaw-droppingly costly.
Still, despite misperceptions about the causes of corrosion and how to prevent it, it’s not especially difficult for marine-industry professionals and boat owners alike to gain a working knowledge of this seagoing malady.
Corrosion is found in many varieties, each of which is specific to different metals. It can range from simple rust on cast iron to aluminum’s poultice corrosion and the crevice corrosion found on stainless steel. But in general, there are two overarching mechanisms that affect most cruising vessels: galvanic decay that takes place between dissimilar metals and damage caused by stray electrical current.
Tip: Sacrificial zinc anodes are attached to underwater metals, such as propeller shafts, through-hull fittings, struts and rudders, as well as heat exchangers.
Galvanic corrosion occurs when dissimilar metals are placed in contact with each other, are otherwise connected via a wire or other conductor, and exposed to an electrolyte, which in this case can be fresh or salt water, or even high humidity. Of these, seawater’s abundant conductivity predictably accelerates the process.
Galvanic corrosion is electrical in nature, though it will occur without an actual power source. Instead, electrons flow naturally between dissimilar metals, much like in a battery, albeit at a very low rate, typically measured in thousandths of an amp.
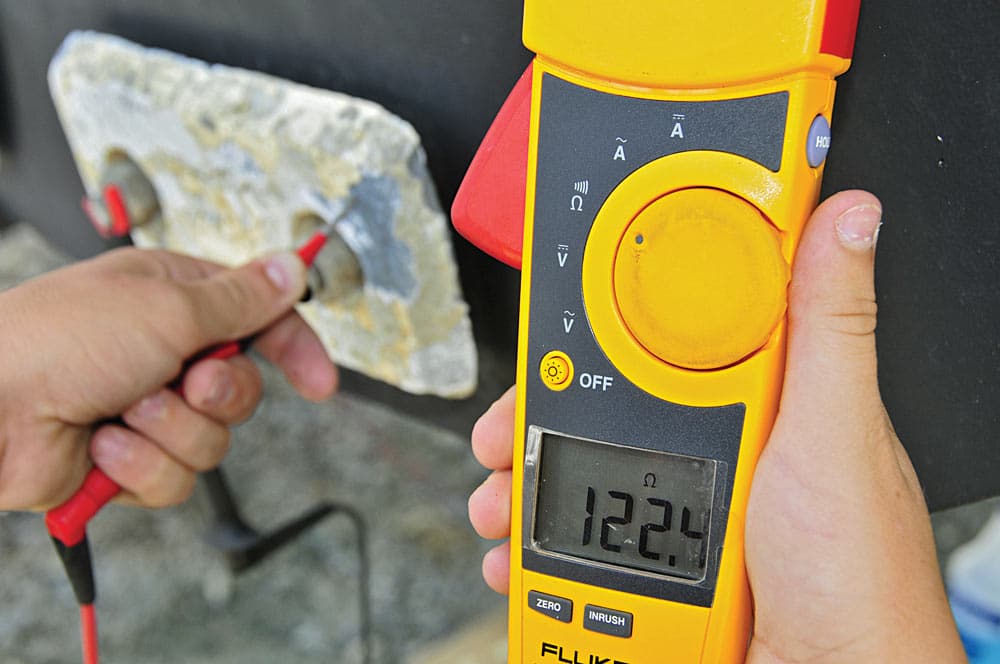
While virtually any two metals will interact with each other in this scenario, those that are further apart on the galvanic series, or scale, will interact to a greater degree, or more aggressively. Metals that are located at the most noble end of the galvanic series (least prone to corrosion) include exotic materials such as graphite, gold and titanium, as well as 316 stainless steel, and nickel-chrome alloys used for propeller shafts. Those toward the least noble end of the scale, magnesium, zinc and aluminum alloys, are significantly less corrosion-resistant, but can be used to protect the metals around them.
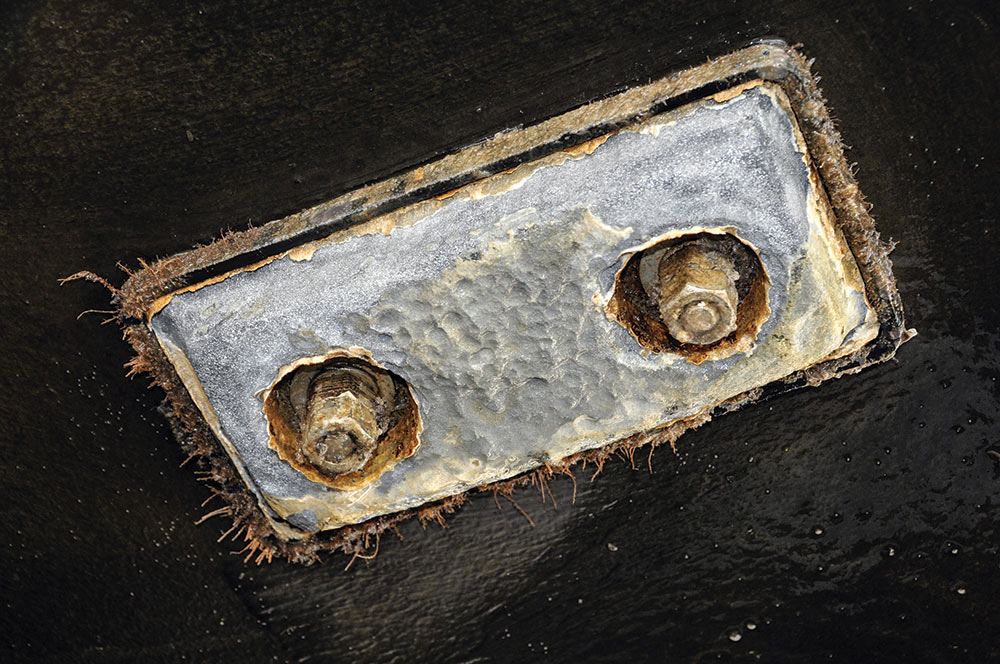
Dissimilar metal combinations that are especially problematic include copper (and copper alloys such as bronze and brass) and aluminum, and to a lesser degree, stainless steel and aluminum. In fact, because of the nether region it inhabits on the galvanic scale, virtually any metal placed into contact with aluminum, and in the presence of moisture, will cause the aluminum to corrode. In 1895, before this phenomenon was thoroughly understood from a boatbuilding perspective, the Herreshoff-designed and -built America’s Cup contender Defender was assembled using a nickel-aluminum alloy hull above the waterline and bronze plate below, laid out over steel frames, with bronze rivets throughout. This created a batterylike galvanic mélange, and it wasn’t long before the boat had to be scrapped because the hull plating had pitted so heavily it was no longer seaworthy (but not before it fulfilled its intended purpose: winning the Cup).
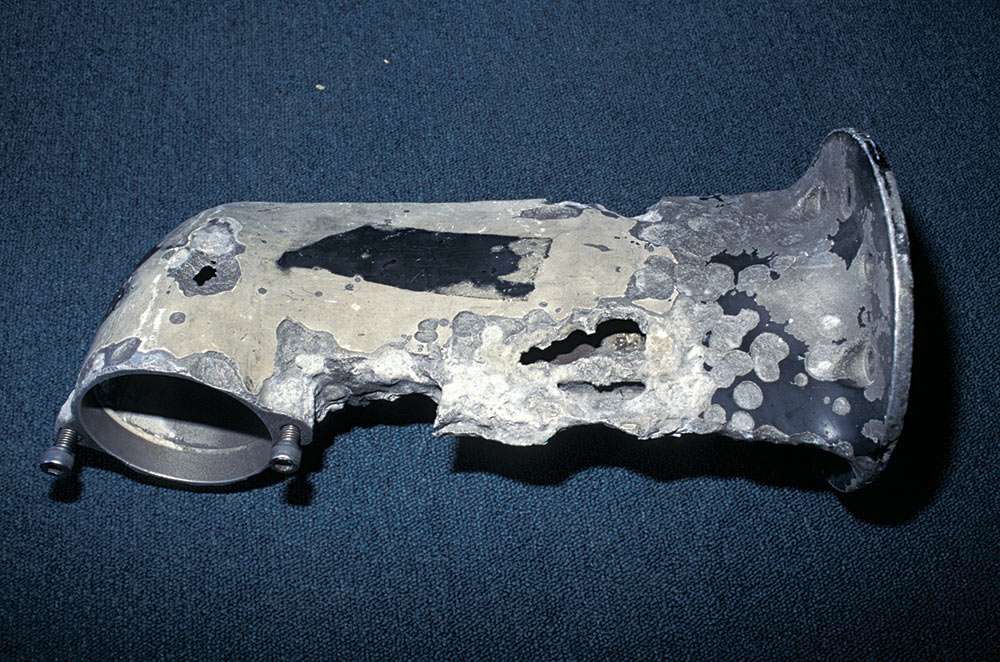
Aboard Your Boat
Examples of galvanic corrosion that can be found aboard the average cruising vessel include brass hydraulic steering cylinders or bronze seawater strainers supported by aluminum brackets; aluminum hydraulic cylinders (often used with outboard motors), which utilize brass hydraulic fittings; and to a lesser degree, aluminum deck hardware or masts and booms that carry stainless-steel fasteners.
However, the very best example of galvanic corrosion is one that’s intentional: Sacrificial zinc anodes are attached or otherwise electrically connected via a bonding system to underwater metals, such as propeller shafts, through-hull fittings, struts and rudders, as well as heat exchangers. Ignoble zinc is one of three sacrificial metals that can be used for cathodic protection aboard vessels; the other two are aluminum and magnesium. Of these, zinc should only be used in seawater; magnesium is suited only to fresh water; aluminum can be used in fresh, brackish or seawater. All three corrode while protecting the metal to which they’re connected.
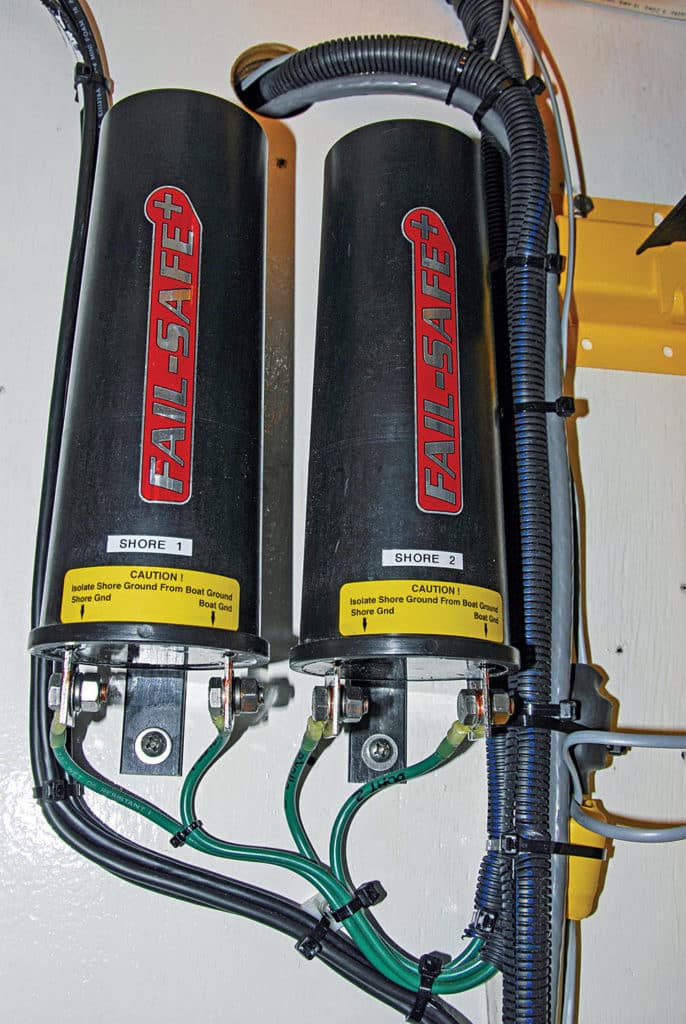
In practical terms, the most effective means of preventing galvanic corrosion is to avoid using dissimilar metals in scenarios where they will come into contact with each other, or where they are otherwise electrically connected. Where this is unavoidable, an insulator can be inserted between them, either a nonconductive material or, in some cases, another metal that is benign to both. Nonconductive materials include prefabricated fiberglass or epoxy-based sheets (but avoid using nonreinforced plastics in highly loaded structural applications).
Stainless steel is often used as an insulator between aluminum and copper-based alloys, say between aluminum fuel tanks and brass (a copper alloy) valves. While aluminum and brass are technically still connected, the stainless-steel bushing provides the necessary degree of spatial isolation; however, this approach would not be acceptable for submerged or continuously wetted components.
The Boats Around You
While galvanic corrosion is typically a localized event affecting the dissimilar metals on a given vessel, it can also occur between boats that are in close proximity. This concept can be somewhat confusing, and is understandably the source of a great deal of misinformation, including the “hot marina” myth.
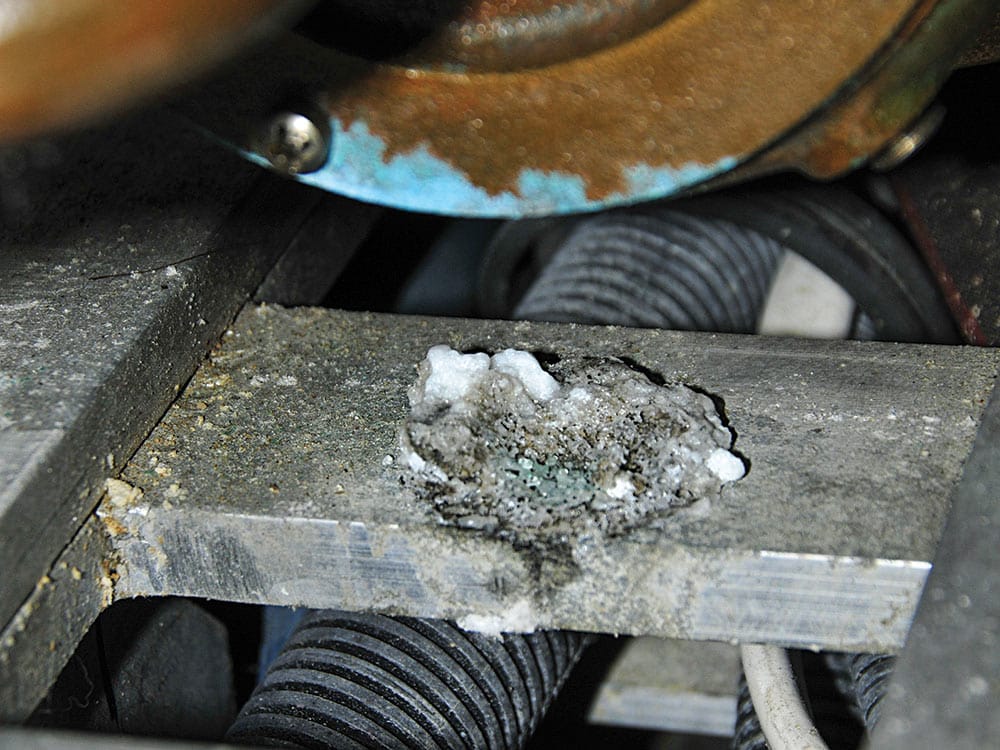
Inter-vessel galvanic corrosion occurs when, for instance, two boats berthed near each other both plug into shore power. In doing so, the green alternating-current safety ground wiring for each vessel becomes connected regardless of whether or not the shore power is energized. (The AC safety ground is tied in with the boat’s direct-current ground wiring and bonding system that’s used to connect underwater metals such as seacocks, struts and shafts. More on this in a moment.)
Tip: Galvanic isolators work by blocking up to 1.4 volts DC (which is above the typical galvanic corrosion-voltage threshold) on the AC shore-power safety ground wire.
To reiterate, as soon as shore power is plugged in, AC safety grounds and bonding systems between vessels are interconnected. When this occurs, intact sacrificial anodes — or less noble underwater metals such as aluminum saildrives — on one boat may begin inadvertently protecting underwater metals on other vessels whose anodes are depleted. Except for the fact that the shore-power cord must be connected, this phenomenon has little if anything to do with the marina, or shore power per se; it remains a galvanic phenomenon.
As insidious as this scenario is, it is easily thwarted using either a galvanic isolator or an isolation transformer.
Galvanic isolators work by blocking up to 1.4 volts DC (which is above the typical galvanic corrosion-voltage threshold) on the AC shore-power safety ground wire. The isolator still allows AC fault current to flow freely, which is critical from a safety perspective. Because galvanic corrosion involves DC current, the electrical interconnection of adjacent vessels is prevented by the galvanic isolator.
Isolation transformers take this a step further by isolating all shore-power connections, including the AC safety ground, between a boat and the dock, thereby blocking any level of inter-vessel conductivity. Every vessel equipped with a shore-power system should utilize one of these devices.
While it is a potentially serious and costly phenomenon, galvanic corrosion occurs slowly, typically over the course of weeks if not months and years. With proper alloy selection, isolation and cathodic protection, it can be minimized if not eliminated.
Stray Current
Stray-current corrosion differs from galvanic corrosion in that it only occurs in the presence of an outside source of electricity, most commonly a boat’s own DC electrical system, battery or battery charger. Shore power, or AC voltage, does not typically cause stray-current corrosion. If it did, the DC-voltage-blocking ability of a galvanic isolator would be ineffective. Rare though it may be, when it does occur, AC-induced stray-current corrosion is of greatest concern for aluminum-hulled boats, as well as boats with aluminum saildrives.
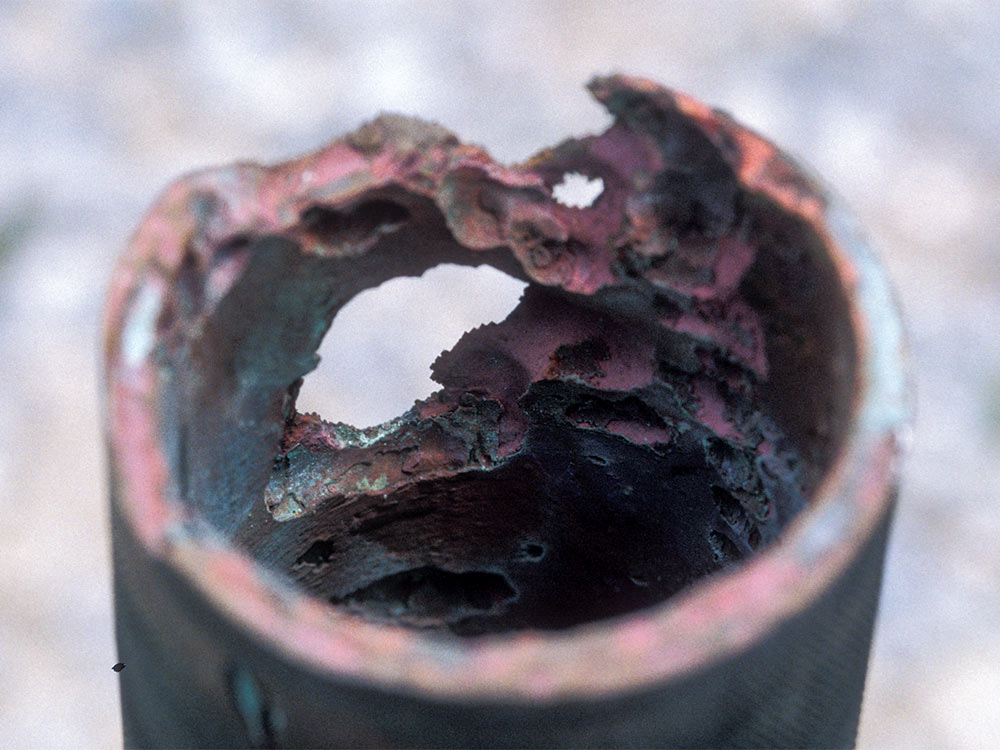
The typical stray-current corrosion scenario involves a faulty electrical connection that is located in, or close to, bilge water, or one that makes contact with a submerged metal. Contrary to popular belief, electricity does not seek ground; it seeks a return path to its source. In the case of a boat, that’s the vessel’s battery. Current leaking into bilge water may travel to a through-hull fitting, then into the water in which the vessel is floating, then on to other underwater metals, which are grounded to the DC-negative system via the engine block, and thence back to the battery.
Tip: The typical stray-current corrosion scenario involves a faulty electrical connection that is located in, or close to, bilge water, or one that makes contact with a submerged metal.
When this occurs, underwater metals will almost certainly suffer from severe and rapid damage. Unlike galvanic corrosion, which occurs comparatively slowly, stray-current corrosion moves with startling rapidity, potentially destroying a propeller, shaft or saildrive in a matter of days.
Sacrificial anodes, galvanic isolators and isolation transformers offer little if any protection against this electrical scourge (isolation transformers can be beneficial for preventing stray-current corrosion that originates on vessels other than the one equipped with the transformer). Isolation transformers prevent stray current that reaches or leaves a boat via the shore-power grounding conductor. However, they do not block current or corrosion in a vessel sitting in the path of a stray current flowing between two boats. This current can pass through a metal hull or its bonding system on the way back to its source, causing corrosion.
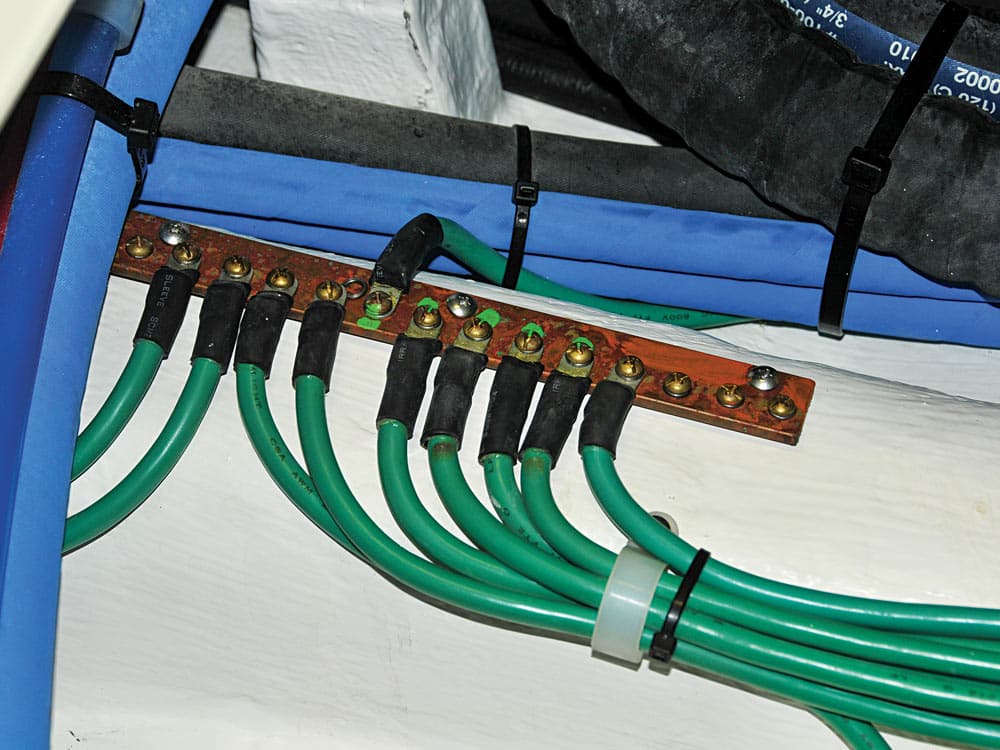
The most effective means of preventing stray-current corrosion is by observing sound, American Boat and Yacht Council (ABYC)-compliant wiring practices, particularly in and around bilge areas.
Bilge-pump and float-switch connections should be made no less than 18 inches above the base of the pump. The primary reason for doing so is to improve reliability; however, this approach also reduces the likelihood of stray-current corrosion. If this is impractical, then connections should be made waterproof using heat-shrink butt splices or stand-alone heat-shrink tubing. If necessary, apply silicone sealant around the connections, and never allow them to languish in bilge water. A detail as seemingly innocuous as improperly crimping, and thereby piercing, a heat-shrink butt splice can create a stray-current pathway.
While particular attention needs to be paid to electrical junctions made in the vicinity of bilges, stray-current corrosion can occur virtually anywhere aboard a vessel where a positive DC conductor makes contact, directly or indirectly, with a submerged metallic structure.
Yet another means of preventing or diminishing the effects of stray-current corrosion involves the use of a bonding system (their installation guidelines are detailed in ABYC Standard E-2, “Cathodic Protection”).
Bonding systems are one segment of a vessel’s overall grounding system, which encompasses the DC negative, AC safety ground and lightning ground systems, all of which are interconnected.
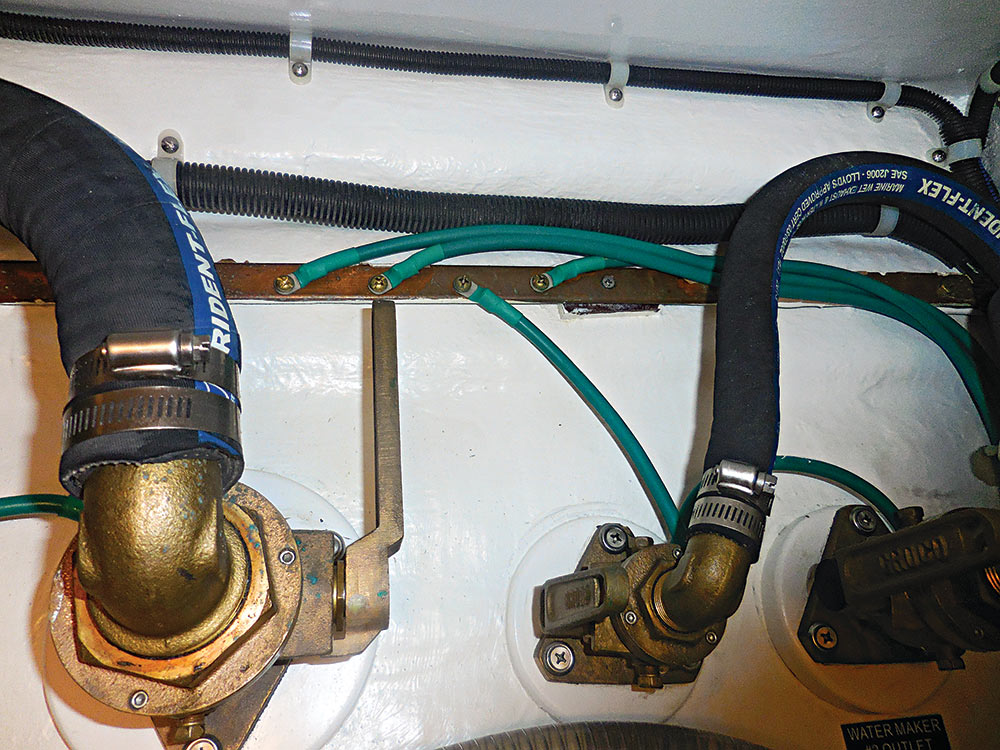
In brief, a bonding system electrically interconnects underwater metals and many metallic machinery components, including through-hull fittings and seacocks, rudder and propeller shafts, struts and strainers. It does this by maintaining all underwater metals at the same voltage. If all metals are of equal voltage, no current can flow between them, and there will be no stray-current damage.
Tip: Stray-current corrosion can occur virtually anywhere aboard a vessel where a positive DC conductor makes contact, directly or indirectly, with a submerged metallic structure.
There are two primary benefits to bonding. First, it can mitigate stray-current corrosion. In the case of voltage leaking into bilge water from a defective bilge pump connection, if the underwater hardware through which the fault current flowed was bonded, all or most of the current would return to its source, the battery, rather than through the water in which the vessel floats, thereby eliminating or minimizing the damage to other underwater metals. It’s the un-bonded hardware that will corrode in this scenario.
The second benefit of a bonding system relates back to galvanic corrosion and its prevention. Bonded metals are nearly always dissimilar (silicon-bronze seacocks, stainless-steel alloy shafts and manganese-bronze propellers, for instance), which violates the aforementioned guidelines on galvanic corrosion. Bonding systems, however, include one additional component in this metal cocktail: a sacrificial hull-, shaft- or rudder-mounted anode.
Connecting underwater metals to each other and then to an anode follows the “bond-and-protect” protocol, a proven approach that works, provided a handful of guidelines are followed. Chief among these is ensuring low-resistance connections are made between bonded components and hull anodes, the standard for which, established by ABYC, is stringent indeed: a maximum of just 1 ohm.
Aboard the vast majority of vessels I inspect, bonding systems, and specifically, their connections, are in abominable condition: They are green, crusty, loose or broken altogether.
Like any other system aboard your sailboat, the bonding system should be periodically inspected and maintained. Corroded or otherwise poor connections should be cleaned or replaced. If doubt exists about the integrity of the system, resistance between components should be checked by using an ohm meter while the vessel is hauled out to measure the resistance between the anode and the metals to which it is connected.
Corrosion — and preventing it — need not be mysterious. While its analysis is often deemed a black art, it is in fact anything but; its causes have been studied and are clearly understood. In most cases, efforts to keep corrosion at bay are within the skill sets of the do-it-yourself sailor. But while the guidelines I’ve outlined will help prevent the most commonly encountered corrosion problems, if you find yourself in over your head, make sure you call in an ABYC-certified corrosion specialist.
Steve D’Antonio is author of CW’s Monthly Maintenance column and offers services for boat owners and buyers through Steve D’Antonio Marine Consulting.