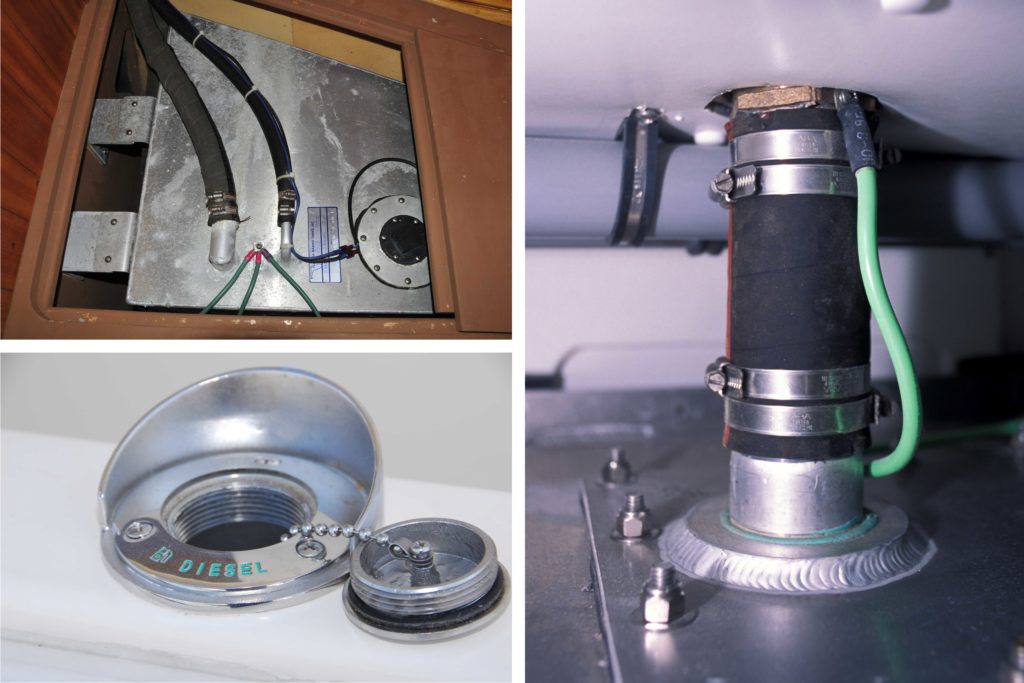
It’s all too easy to take for granted that fuel will make its way from the deck fill to the tank and from the tank to the engine. The means by which fuel travels and the plumbing it uses to make this trip often go overlooked until a leak or other failure develops.
While fiberglass, metallic pipe or plastic are acceptable (with limitations), the connection between the deck fill and the tank is nearly always made of a rubber or rubberlike hose. Hose is convenient in that it can be easily routed and it absorbs movement between the deck, hull and tank. Hose used in this application is far from ordinary. It must carry a U.S. Coast Guard A2 rating, which means it’s designed to, among other things, resist exposure to flame for a minimum of 2½ minutes.
Typically, this hose is also reinforced with wire to prevent kinking and crushing. Where American Boat & Yacht Council compliance is sought, fuel-fill hoses must also be installed with double clamps (this is one of only two locations where ABYC Standards mandate double clamping; the other is exhaust systems), which are all stainless steel, including the screw, and whose band width must be a minimum of a half inch.
Fuel-fill plumbing must be self-draining; it should avoid horizontal runs and dips, because they tend to make for slow fueling, while promoting air “blowback.” All metallic components in the fuel-fill system that are in contact with fuel, including the deck fill and tank, must be grounded, with resistance between these components and the vessel’s ground not exceeding 1 ohm (in other words, very low resistance). The grounding wire used for the deck fill must utilize a machine screw, i.e., a nut and bolt, rather than a tapping screw; the wire cannot be clamped between the hose and deck-fill pipe.
Fuel tanks must be vented to allow air to escape while filling and enter as fuel is used. Vent plumbing typically consists of hose that should, if it passes through the engine compartment, carry a type-A1 rating. It must be run in such a way as to ensure it does not trap fuel (no dips or low spots), using a continuous run upward from the tank to the vent. The vent plumbing must connect to the highest point on the tank, which may call for dual vent connections to ensure it remains so while motorsailing (these can be T’d so only one exterior vent is necessary). The vent itself must be located above the fill or the hose run must incorporate a riser, an inverted U, as close as possible to the vent. This arrangement will (or should) prevent fuel from being pushed out the vent before it reaches the filler nozzle at the deck fill during filling, while minimizing the possibility of water being pushed into the vent. All fittings and connections associated with the fill and vent plumbing must be readily accessible (joiner work should not require significant disassembly).
Vent placement itself is critically important; more than a few vessels have been plagued by water being ingested into fuel tanks via a poorly placed vent. Vents should not be installed on hull sides; in addition to risk of submersion, this would frequently place them below the fill unless they were equipped with a riser.
The O-ring on the deck fill should be inspected regularly, and replaced if it shows any signs of deterioration. Periodically lubricating it with Teflon grease will extend its life and improve the seal it makes, keeping both rain and seawater out of your tank. Finally, the deck-fill cap should be connected to the filler neck with a chain or wire.
Next month, we’ll review fuel-supply plumbing.
– – –
Steve D’Antonio offers services for boat owners and buyers through Steve D’Antonio Marine Consulting (stevedmarineconsulting.com).