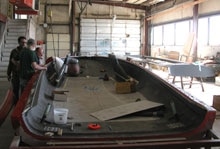
NHGoetzA
In addition to not being in Cranston, a benefit to working for a boating magazine in Newport, Rhode Island, is that it’s pretty easy to cook up a reason to get out of the office and go on an important fact-finding mission.
Take the other day, for instance, when on a sun-splashed early spring morning, I managed to get dispatched to nearby Bristol to wander through Goetz Custom Boats with John Boone, director of sales and market development, and marketing maven Sara Watson McKay.
Now most of the time, a trip to Goetz would be more appropriate for one of my colleagues down the hall at Sailing World. After all, most of the carbon-fiber hulls the company cranks out are being built for guys who are cutting off toothbrush handles to save weight, not bringing bikes, kayaks, windsurfers and barbecues aboard to keep the party options open.
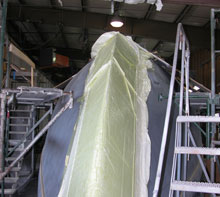
Mark Pillsbury| |The epoxy pre-preg hull of the Morris 56 is in the midst of its layup| But as luck would have it, Goetz was in the process of laying up a 56-foot Ted Fontaine-designed glass and epoxy, vacuum-bagged hull for Morris Yachts. So, with a cruising boat on the floor, I finally had my foot in the door and a reason to go calling. According to Boone, when a company like Morris gets an order for something that’s not right up their alley (epoxy in this case), Goetz will get the call. They specialize in one-off projects that require the building skills that a few America’s Cup campaigns have helped hone. Once completed, the hull will be shipped to Maine, where Morris will finish the custom build.
The first thing I noticed once I got past the offices and into the boat-building portion of the 23,000 square-foot building, was how clean things were. That’s not an accident. Along with developing the tooling and skills needed to construct boats on the bleeding edge, Boone said the company’s had to develop ways to safely work with epoxies that can kill you if you’re not careful.
The second thing I noticed was the still-in-the-mold hull for an A-Scow and its deck, nearby, also made from carbon fiber. While it looked like it would be a tough boat on which to rig a hammock, I got the feeling it would be a pretty cool boat to sail on a breezy afternoon. Farther back in the shop, guys were installing fittings on a new TP 52, due to be shipped off shortly to a Spanish team in the Med. Goetz was chosen for the build, said Boone, because the owner backed up the days from the start of a particular regatta and knew the boys in Bristol would have the boat on the line and ready to sail by race day.
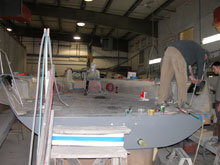
Mark Pillsbury| |Workers add hardware to a TP52| There was another big boat, its carbon-fiber hull still upside down in the oven next to the TP. The boat’s destined for local waters, but details about it were hush-hush (a camera would have been a faux pas). Obviously someone’s planning to make a splash on the starting line sometime soon.
Upstairs, Boone led the way to the shop where smaller parts are manufactured. Molds are cut by a CNC machine and then cloth and carbon are cut to suit. A laser connected to a laptop sits overhead, projecting colored lines that tell workers where to cut and place each piece; the direction of the weave is also specified to meet the designer’s plans.
There will be a lot more of these light-driven devices in the new 43,000-square-foot building that’s due to open just down the road in late summer. The plan is to someday soon locate these lasers inside a hull so that there’s no guesswork when it comes to installing bulkheads and other internal parts. The new building will also house a six-axis CNC machine that can cut up, over, under, and around any squiggle a designer wants to draw.
The new building will allow the company to expand its mold business, says Boone, and also will provide space to move deeper into the powerboat market, where owners have been slower to demand boats built with advanced materials and epoxies.
And then there’s this other job the company’s looking at, one that came via an acquaintance in the cruise ship industry. Boone said they’ve been asked to look into building some 30-foot carbon fiber limousine launches for a luxury liner.
Bottom line? It was definitely better than a day spent in the office.