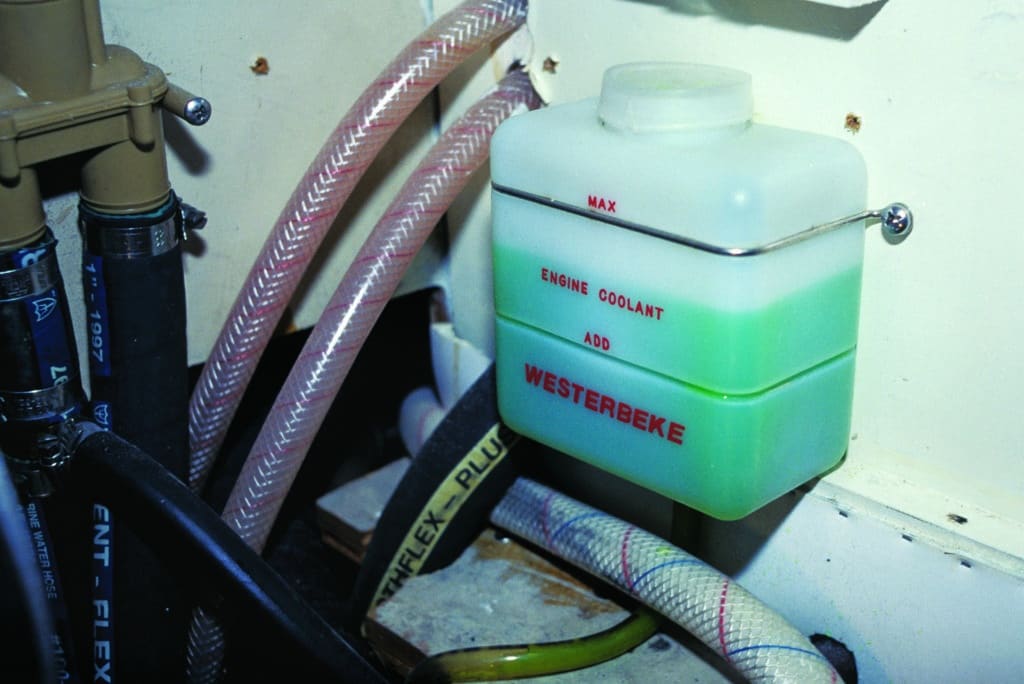
Yet another component that too often is given short shrift by boatbuilders and boat owners, the coolant recovery tank does more than just prevent spills — it also provides a window to your engine’s cooling system.
Closed or pressurized cooling systems offer several worthwhile benefits: They raise the coolant boiling point, keep the system free of air and reduce cavitation. Cavitation can scour metal from cooling passages, weakening engine blocks and cylinder heads, and lead to premature circulator-pump failures.
From a pressure perspective, for every pound of pressure under which the coolant recovery system operates, the boiling point of the water-coolant mix is raised 3 degrees Fahrenheit. (As the boiling point of coolant varies with concentration, the boiling point of water is used for reference.) Therefore, a 15-pound pressure cap raises the boiling point 45 degrees F, affording an additional margin against boiling and overheating.
Most closed cooling systems operate at somewhere between 6 and 15 pounds per square inch. The pressure is maintained and regulated by a pressure cap, which is typically located on the cooling system’s metallic expansion tank (some tanks may be remotely located above the engine if the vessel’s water heater heat exchanger is located above the main pressure cap). Pressure caps are typically embossed with a pressure rating that’s calculated by the engine manufacturer. Under no circumstances should a pressure cap be replaced with one that hasn’t been specified by the manufacturer.
Pressure caps that are designed to operate with coolant recovery bottles include two rubber gaskets, two springs and a check valve. In practice, once the engine is in operation the coolant heats up and expands; when it reaches the pressure rating of the cap, the primary spring is compressed, allowing coolant to flow through the filler neck and into the discharge spout. If the spout is connected to a coolant recovery bottle via a length of hose, the coolant will be captured.
After the engine is shut down, the coolant will cool and contract, creating a vacuum within the cooling system. When a high enough vacuum is achieved, it overcomes the second spring in the cap, the one that’s associated with the check valve. Coolant flows from the recovery bottle, past the valve and back into the engine’s cooling system, keeping it full and air-free. Caps and the filler necks into which they are screwed should be inspected periodically; look for deterioration of the rubber gaskets, broken springs, corrosion, dents or cracks.
Coolant Recovery Tank Tips
Provided the proper cap is used, a recovery bottle can be added to any closed cooling system. Regular inspection of the bottle is key. When the system is operating properly, coolant should always be visible in that translucent recovery bottle. Most bottles have level lines for “cold” and “hot.” The recovery bottle should not be used to top off or fill a cooling system; that must be done via the pressure cap. Once the bottle’s full, however, it will serve as a valuable level indicator.
Note the level of coolant in the bottle when the engine’s cold. Once the engine reaches operating temperature, the level must rise. If it doesn’t, the system is not operating properly. After the engine is shut down and cools off, the coolant level should once more return to the same cold level. If it sinks lower, the engine is leaking or consuming coolant. If you are forced to top off the coolant in the system repeatedly, or if the coolant level never moves within the bottle, it indicates that a problem exists.
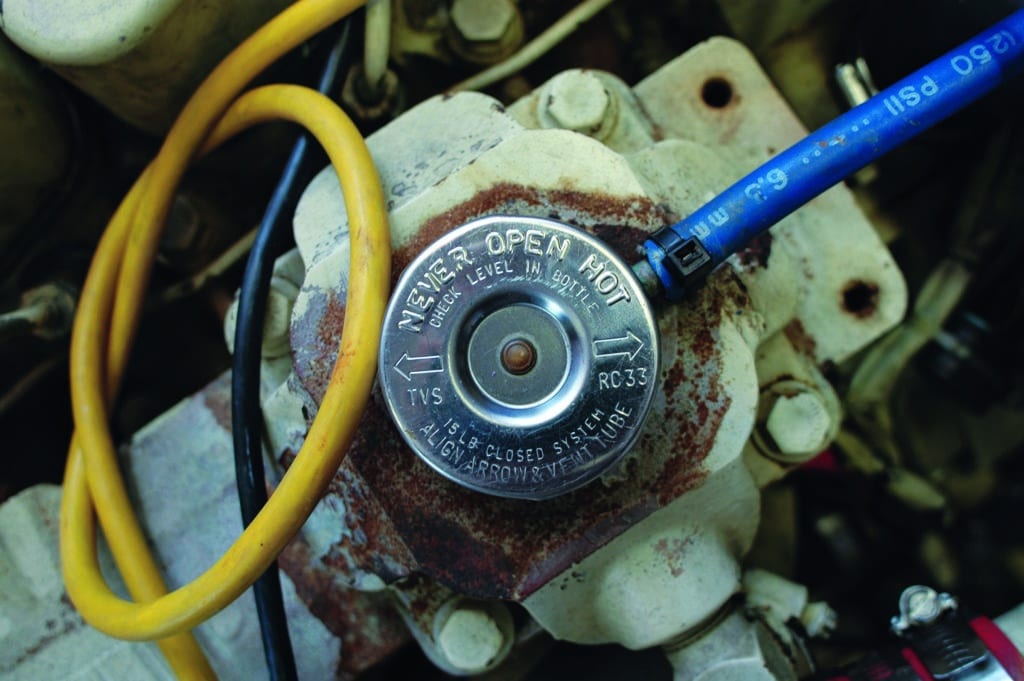
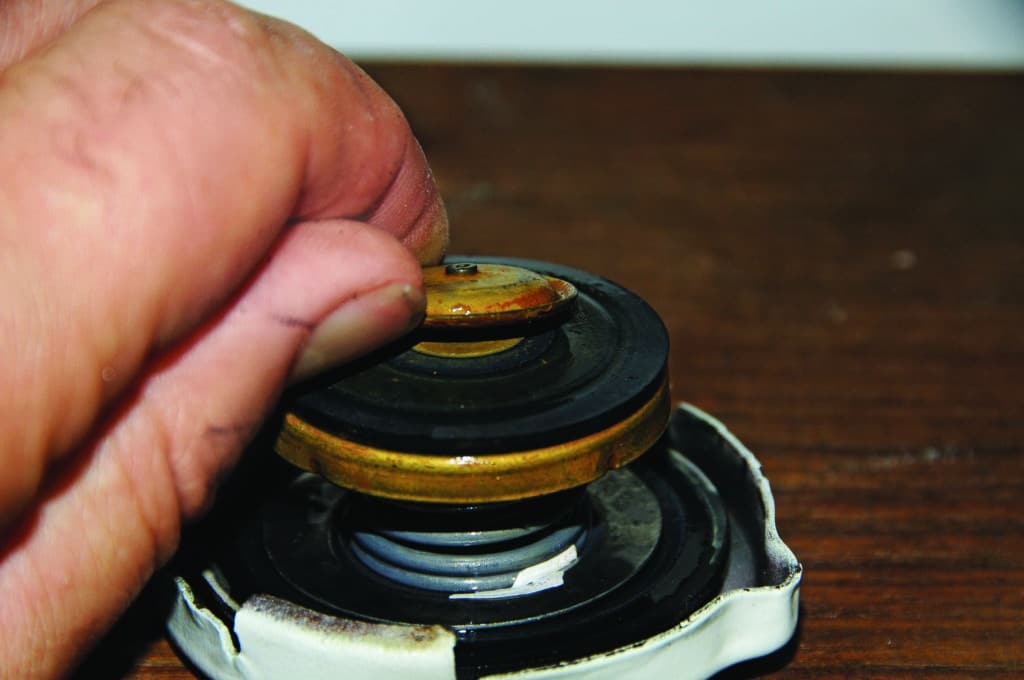
Finally, recovery bottles do not rely on gravity, which makes it unnecessary to mount them above the pressure cap. Instead, they should be installed so that the bottle’s cold-level mark is no higher than the pressure cap. With this approach it is possible to remove the pressure cap for inspection purposes without coolant flowing from the recovery bottle and out the pressure-cap filler neck.
Steve D’Antonio offers services for boat owners and buyers through Steve D’Antonio Marine Consulting.